Automate Sales Order Marking to Avoid Unlisted Transactions
Mark Orders | Inventory Marking | Dynamics AX | Sales Order
Once a month, our specialists receive queries on marking transactions for clients’ purchase and sale orders to set up cross-docking. Most of those sales tax cases encompassed the same issue of getting no marking for orders, despite checking marking in the cross-docking template. Interestingly, the demand requirements section only identifies what is required to create cross-docking. Therefore, they needed to mark demand and supply manually against each other to initiate their cross-docking activities. This was a big company that recently shifted to Dynamics AX. At Dynatuners, we often have similar functionality concerns, yet no comprehensive description is available for marking orders.
This article summarizes the knowledge and experience of marking sales order, purchase orders, transactions, production orders, sales tax and inventory journals. Markings have been stayed unchanged since the earliest version of D365 and AX. So, to begin, we will explore the fundamental concepts on how Dynamics manages and generates data markings to enhance warehouse operations.
Inventory Marking in Microsoft’s Dynamics
The working mechanism of inventory marking involves links in the database between your supply and demand transactions. You will see a similar connection between pegging and the Master planning module. However, you can edit the pegging after running material resource planning. While marking an order is somewhat a permanent link that you cannot remove manually. However, it is a compact link between two transactions.
item number. However, it has no effects on items with standard costs, but for FIFO (first-in-first-out) and LIFO (last-in-first-out), markings will overrise anything the system would perform following FIFO or LIFO. The Marking of order increases the precision of costing by FIFO, turning it into an actual cost. With markings, you can perform inventory tracking for supply orders that are against specific transactions. The below figure describes the cycle for order resource, warehouse management system, distributed order management:
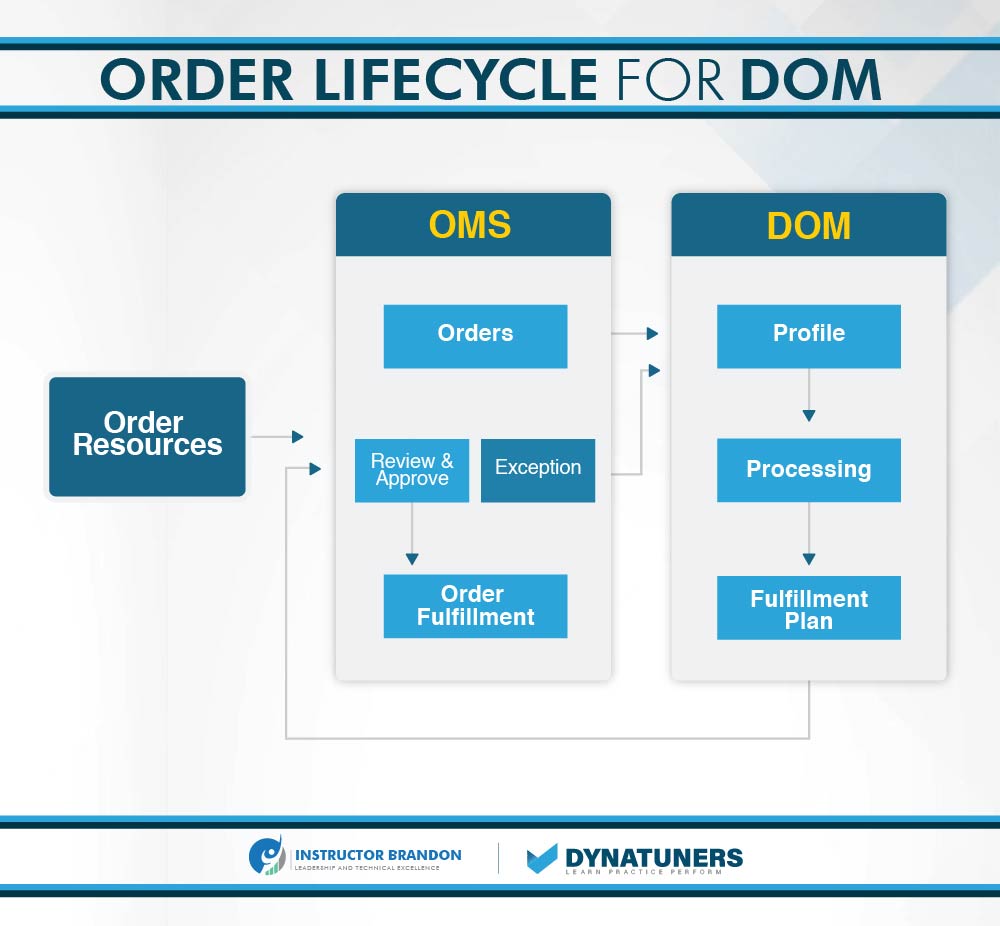
SUMMARY
Marking creates links in the logistics and supply chain. This supports prime functionality in many functional areas. For example, a marking link always makes an ordered reserved transaction, which is not accurate the other way around.
System Generated Markings
There are several scenarios in AX that require the markings of an order. You have to go through markings whenever perform warehouse work with logistics and cost reasons. Bellow are some of the typical scenarios for markings:
- You must mark subcontracted purchase or production orders to the production Bills of Materials line for finished production orders.
- Mark sales order line with direct delivery purchases.
- Production orders for lower-level components created during Estimation are marked to the parent production lines when utilizing line type “pegged supply” in the BOM.
- Return purchase order lines made from the original PO line use marking for the original PO line.
- RMA (Return merchandise authorization) lines created from copying the original sales line are marked as original sales line.
NOTE: Intercompany purchase order lines and intercompany sales lines do not use Marking. There are no item references in the product tab, either. Instead, intercompany authorities have their own set of action links in the action bar.
SUMMARY
Using Microsoft Dynamics AX, you can manually remove system-generated Marking, but it would break the functionality. Users come across several scenarios where removing a marking link is necessary to solve the concerning issues. But it’s infrequent; you don’t deal with system-generated Marking every day. However, if you do so, we can make necessary adjustments within your workspace to remove system generated markings.
Markings Vs. Reservation
Put it simply, reservations are there to reserve your stock for the inventory, whereas markings are to mark your cost on those inventories. Let’s look at how reservations and markings work together.
Here is our detailed blog on inventory reservations, to know more on how it works.
We have a sales order line that is tagged and earmarked for a specific purchase order line in our case. Now, the reservation will hold merchandise from the purchase order for the sales order line. Finally, the marking will connect the cost to the sales line and link the sales and buy lines.
The purchase line will reference the sales line, and the sales line will reference the purchase line.
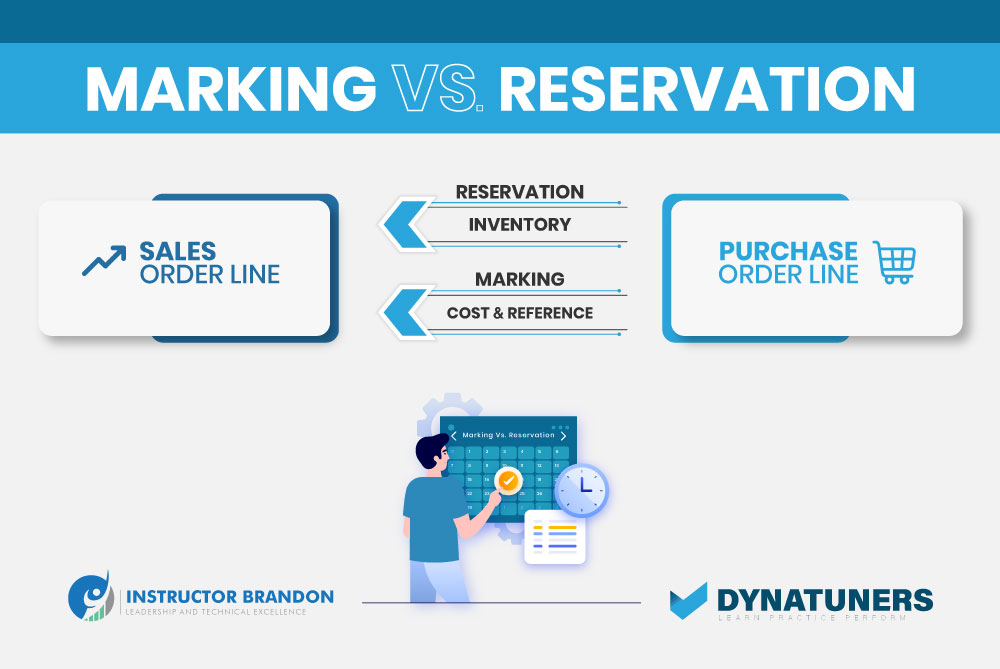
Order Marking in Master Plan
When you go to Master Planning, you have the option of using Marking, Standard Marking, or Extended Marking when setting scheduled orders. However, some users may update the system to enforce the Master Planning parameters value for all users.
We offer better customization to link the marking parameter to groups. As a result, it is easier to identify item numbers involved in Mark-to-order or Engineer-to-order scenarios.
When to use Standard Markings? Well, these are only relevant when your supply order quantity exceeds the demand. The contrast of extended Marking has nothing to do with the marking link itself. Either way, you will still see the link on the marking screen.
However, you will not see the item references with standard Marking while dealing with over-supply. It is not advisable in MTO (Mark-to-order) scenario; we want a sales order reference on a production order, even if it has a larger quantity than the sales line. Typically, the amounts would match with each other. It will help if you utilize extended marking to maximize visibility.
NOTE: The value of this parameter is not enforced. For the user default, it merely supplies the default value. The user defaults determine the value of the marking parameter. Once a user confirms that “Marking = no” is correct, the screen will always default to ‘no’ for that user.
SUMMARY
You can use both standard or extended Marking to view sale order references on the production order as per your ease of use. However, we advise moving towards customization to link marking parameters with groups.
Recalculations & Close Functions
Inventory’s Recalculation and Close functions work together to settle the quantity difference between the two transactions.
When performing the Recalculation and Close capability in Microsoft Dynamics AX, it usually applies the costing method set on the item’s model group.
However, the system will override the standard pricing method available on the item’s model group if you enable the Marking functionality.
While going through warehouse process in inventory management, you need to some transactions to return in the exact cost you first issued. Therefore, you need to allocate some sales orders with specific lot costs. To understand more clearly, let’s go through a scenario.
Inventory Marking Cost Structure |
|||||
Date | Quantity | Cost per Product | Status | Running Total Cost | Average Cost |
6/27/2020 | 5.00 | 100.00 | Initial Balance | 500.00 | 100.00 |
7/09/2020 | 4.00 | 110.00 | Purchase-Receiving | 440.00 | 531.42 |
7/15/2020 | 1.00 | 100.00 | Issuance-Marking | 200.00 | 106.67 |
7/19/2020 | 1.00 | 102.86 | Issuance | 205.72 | 102.86 |
7/27/2020 | 1.00 | 110.00 | Sales-Marking | 220.00 | 110.00 |
We have an initial balance (Qty=5 @ $100), Inventory reception from a purchase order (Qty=4 @110), so the average cost is (500+440)/(5+4)= 104.44.
An issuance needs to be issued at the cost of the initial balance. Then, another issue will be given at the current average price. Finally, in the end, a sales order needs to be issued at the cost of the purchase order.
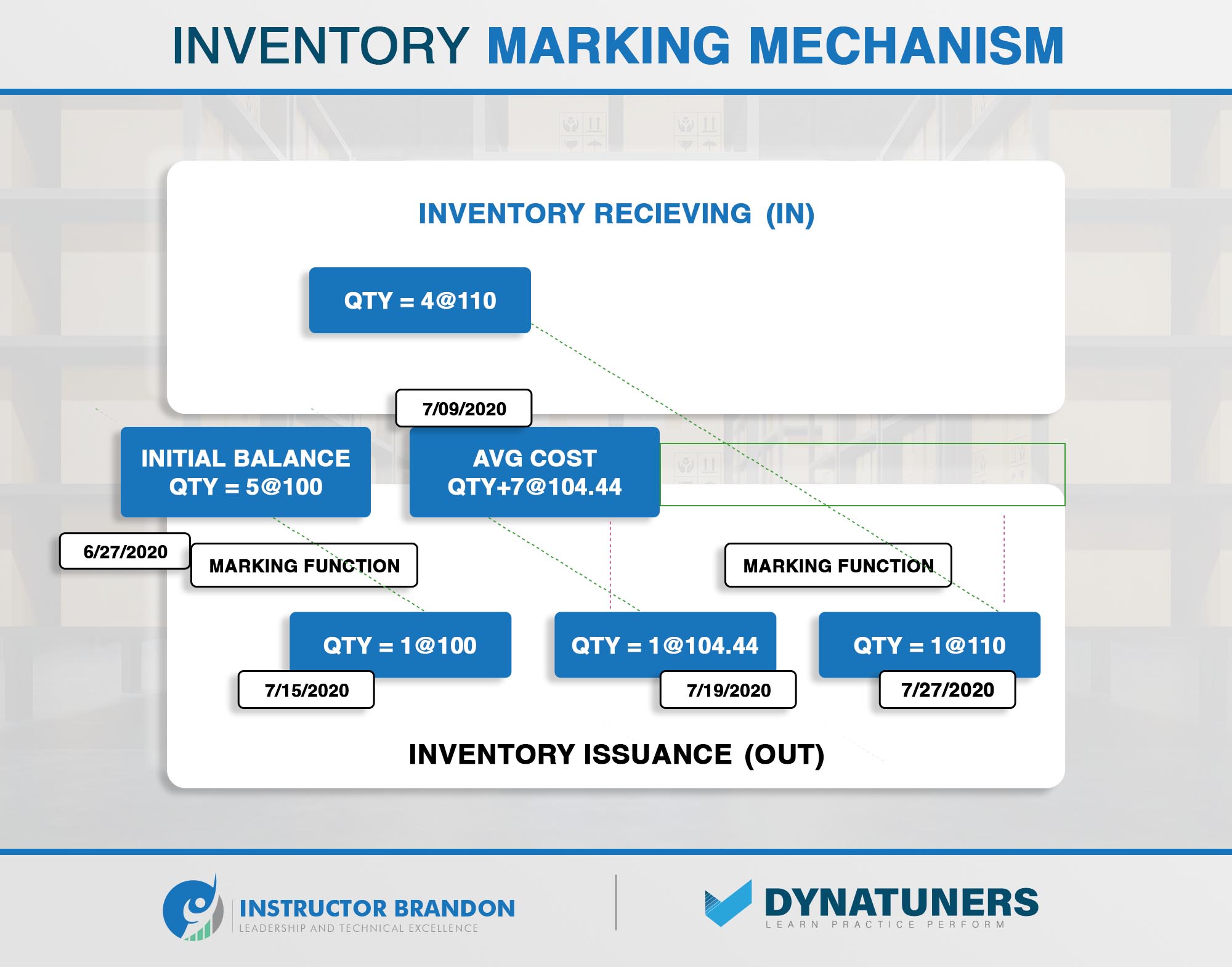
The built-in transactions Lot IDs in MS Dynamics AX provide the marking mechanism; the function may be found in any inventory transaction form (Purchase Order, Sales Order, Inventory Movement, etc.).
The marking function can be done either manually or automatically.
Automatic Marking
– When generating a credit note that will withdraw quantities from the warehouse at the exact cost, use the Purchase Order return.
– A sales order that is linked to a purchase order, with the cost of the sold quantities being added to the price of the received numbers.
Manual Marking
– A specific receiving transaction could be explicitly assigned to a sales order line.
– Movement Journal In/Out could be manually associated with a particular reception transaction.
Marking Relationships with Pegged Supply
Pegged Supply is a BOM line order type that only builds links between manufacturing orders, but it does so considerably later than Master Planning. Firming planned production orders with marking set to ‘standard’ or ‘extended’ can achieve the same end effect. The most significant distinction is early visibility. Because the orders do not exist yet, you will have no view of lower-level Production orders until you estimate the top-level production order with “Pegged Supply.”
This could be a good argument to go with regular planned production orders firmed up with Marking.
Customers are frequently concerned that Pegged Supply will prohibit the MRP (Material Requirement Planning) run from generating planned purchase orders below the “Pegged Supply” item.
This isn’t an issue. MRP will execute the BOM explosion as usual. Still, instead of conventional planned production orders when it sees “Pegged Supply,” it will construct “directly derived” planned production orders that display as “Dynamic.”
SUMMARY
MTO and ETO companies should employ Marking as a vital logistic function. Without a project number, it resembles “project manufacturing.” When using standard costing, the system-generated Marking works the same way, but the user cannot mark anything manually. This problem can be solved with a bit of code update.
Mark Order through PO Using Dynamics AX
Step 1
Open the sales order, purchase order, transaction, production order, or inventory journal from which to mark orders.
- Go to Sales and marketing > Sales orders > All sales orders. Select a sales order. On the Action Pane, click Edit.
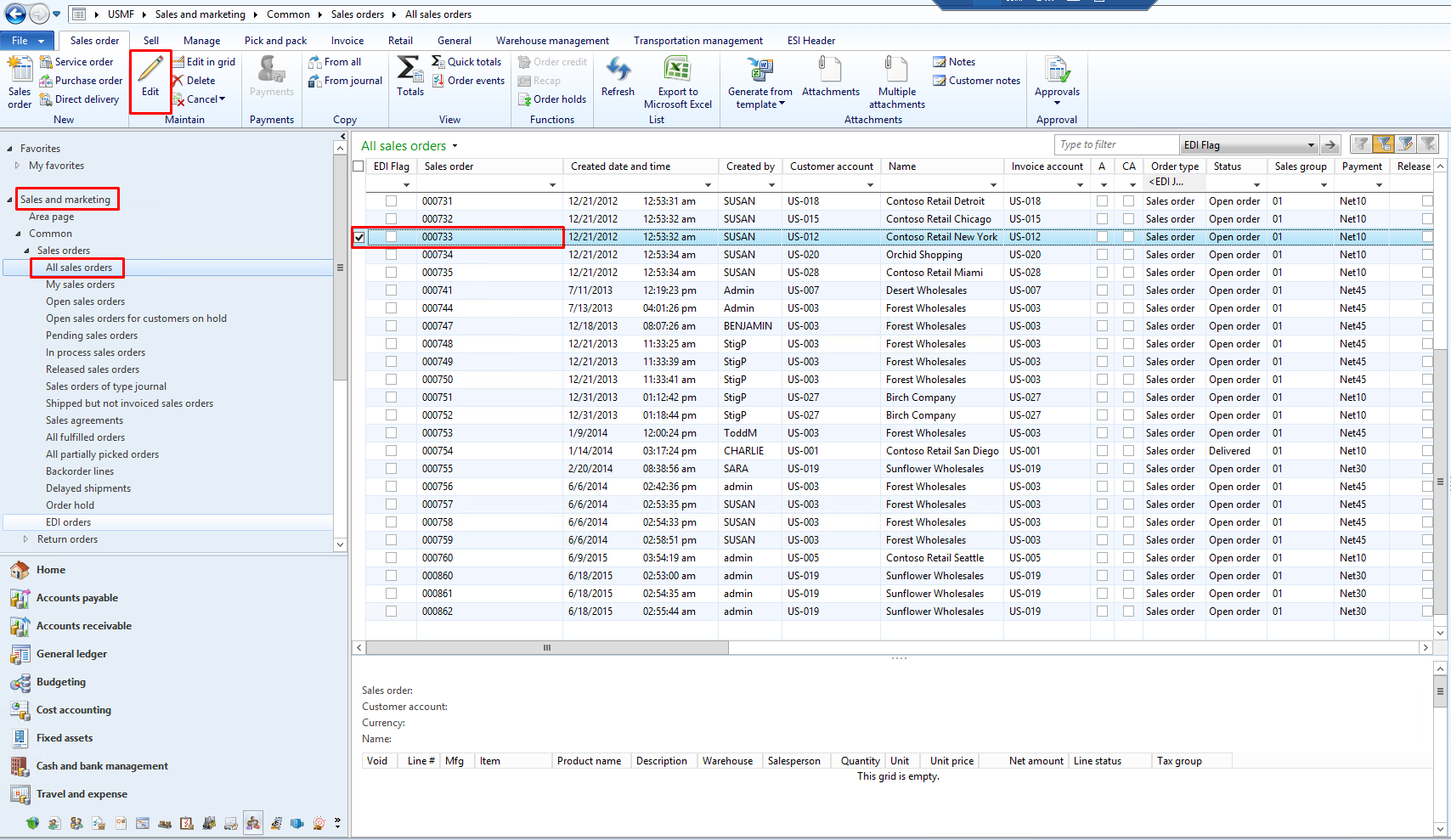
- Click Procurement and sourcing > Purchase orders > All purchase orders. Select a purchase order. On the Action Pane, click Edit.
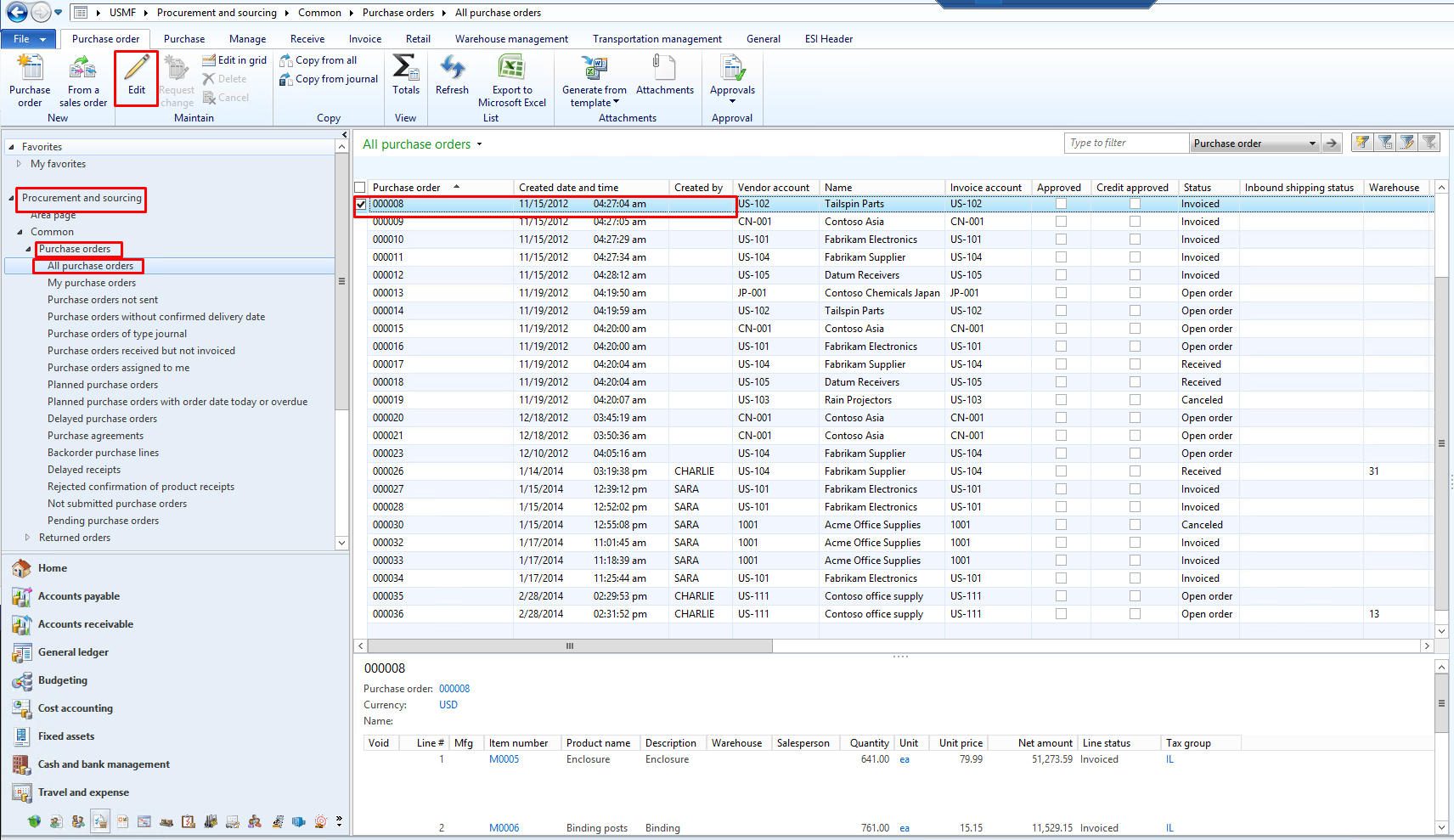
- Go to Product information management > Released products. Select a released product. On the Action Pane, on the Manage inventory tab, in the View group, click Transactions.
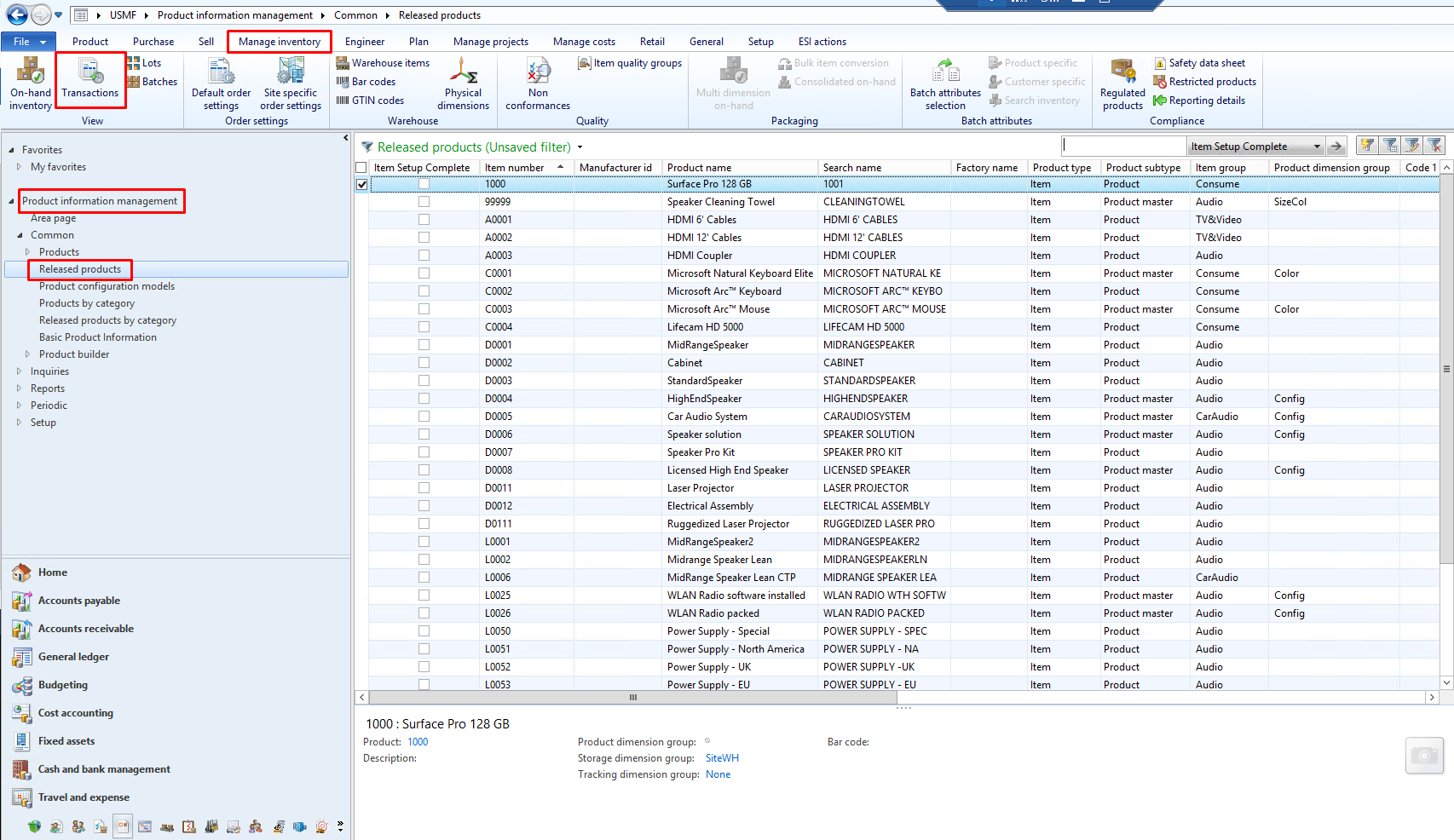
- Select Production control > Production orders > All production orders. Select a production order. On the Action Pane, select Edit.
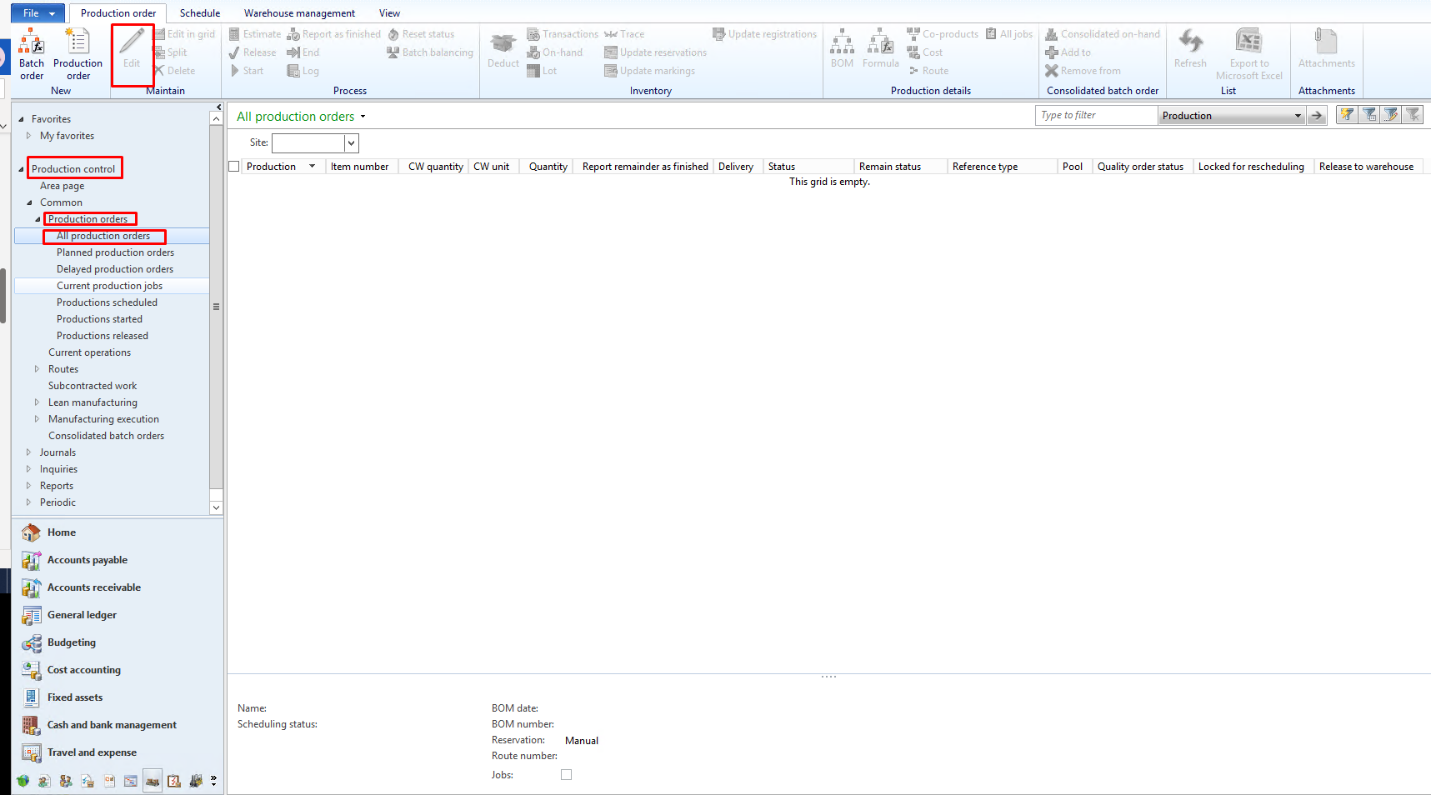
- Click Inventory management > Journals > Item transactions. Click Movement, Inventory adjustment, or Bills of materials, and then click Lines to open a journal lines form.

Step 2
Select a sales order line, purchase order line, inventory transaction, journal transaction, or production line.
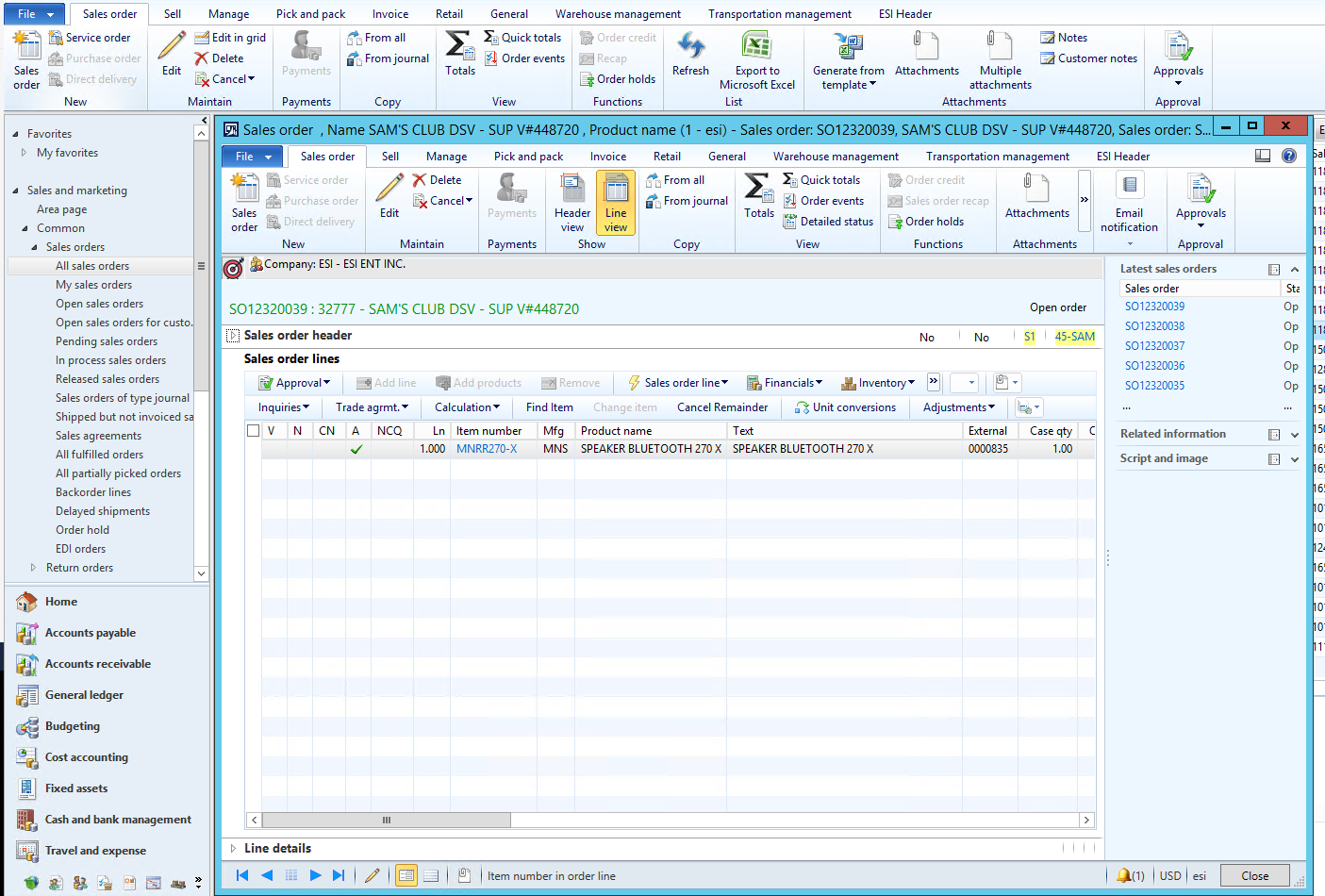
Step 3
Go to Inventory > Marking.
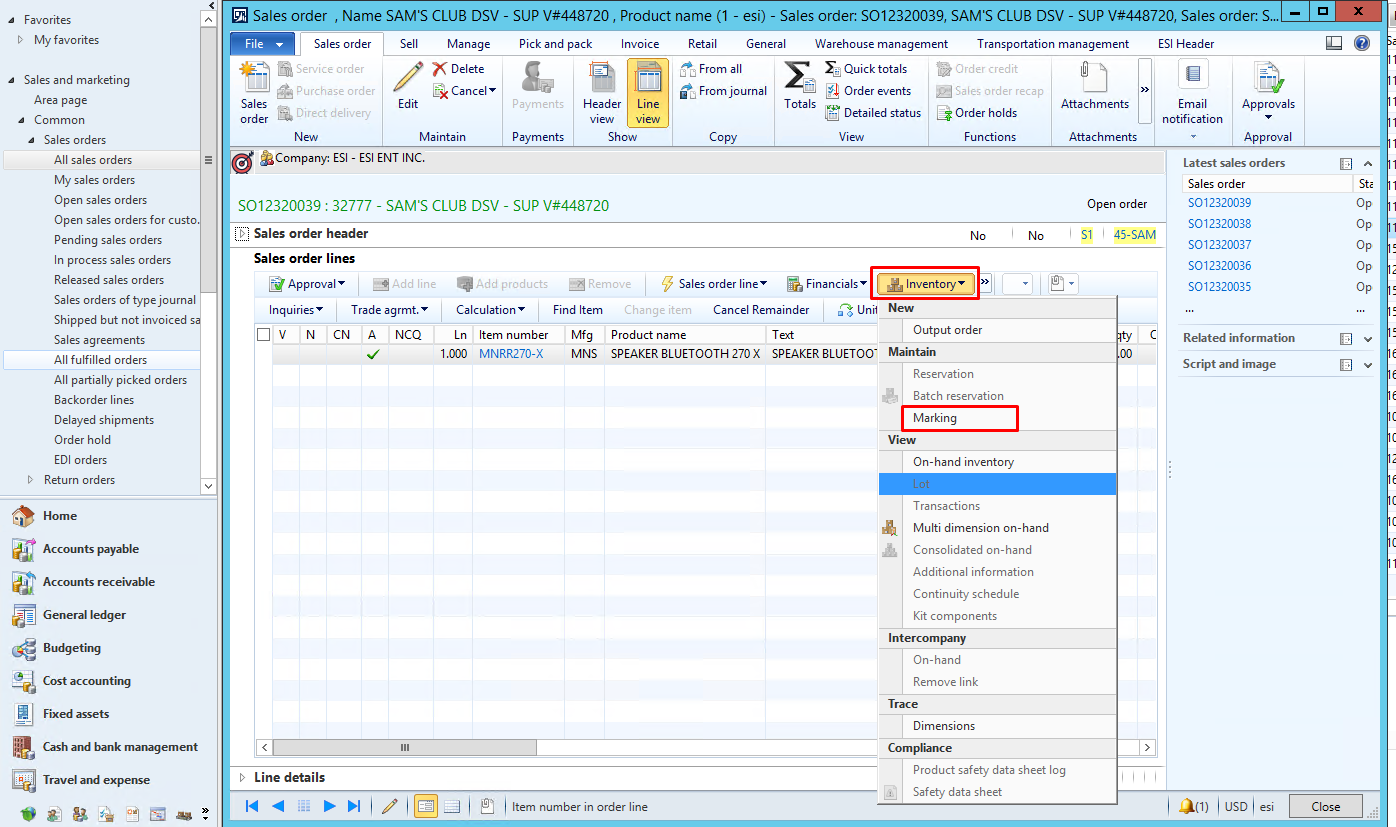
Step 4
Select the Set mark now check box. The Mark now field automatically displays the available number of items or select Auto to automatically suggest orders for marking.
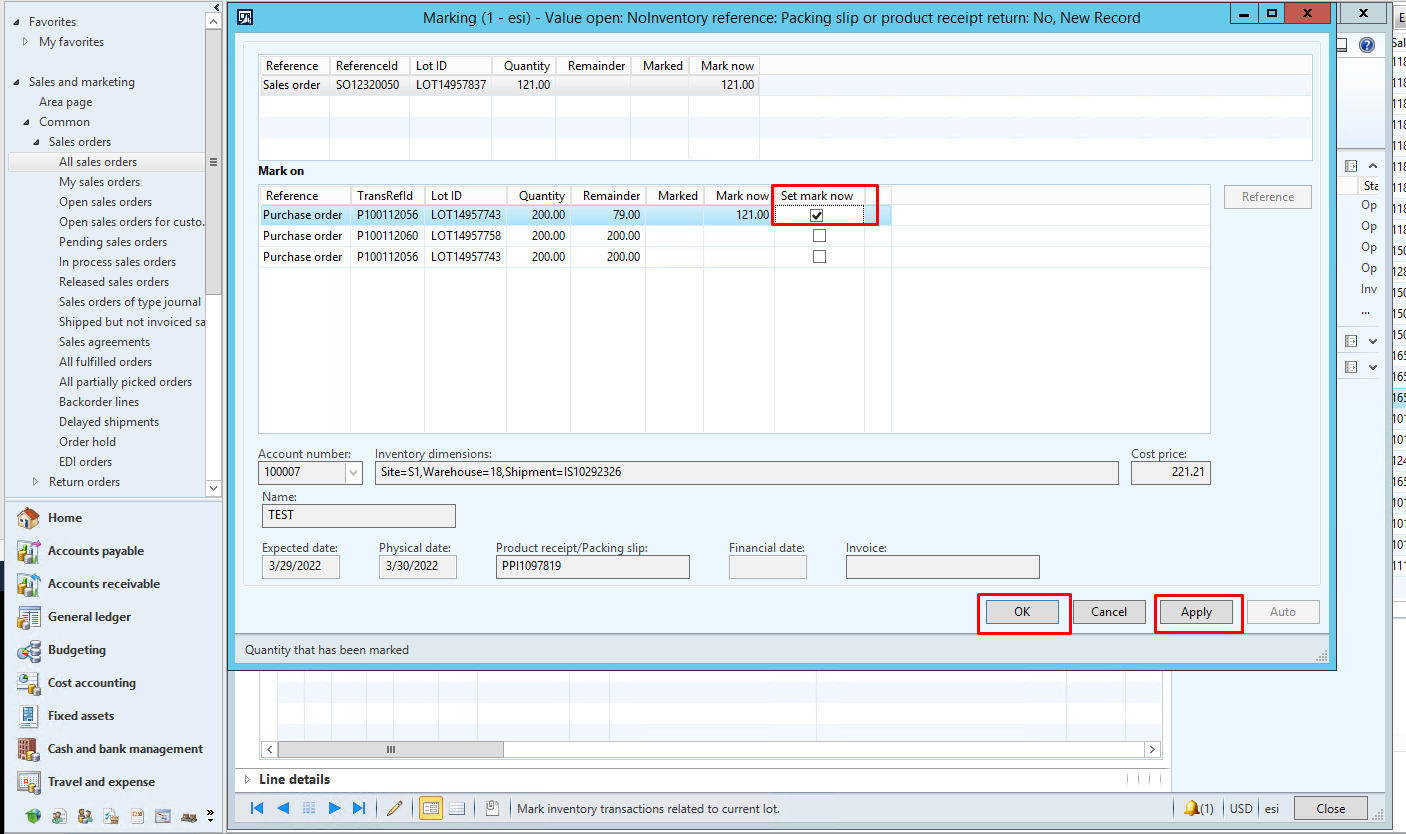
SUMMARY
You can make a connection to an existing purchase order or override the previously assigned linkage by going to the Marking form from the sales order line. Moreover, you can also get to the Marking form by starting with a purchase order line and linking it to an existing sales order line, as done above. You can also override a previous linkage assigned to a different PO or SO.
Bottom Line: Sales Order Marking
The sales order and the item’s supply order must be linked in many circumstances. The marking feature in Dynamics AX is the foundation for detecting related orders. However, the development of linked orders and the usage of marking functionality varies depending on the scenario and whether the products are standard cost or actual cost.
This article evaluated numerous scenarios and recommended using marking functionality appropriately, including manual marking for actual cost items. It went over subjects such as a breakdown of actual costing, reserves, and the Marking usage when firming anticipated orders in greater detail. It also included guidance for scenarios that do not necessitate order linking. The goal was to shed more light on a complicated topic, an essential component of many games plans requiring order linkage.
At Instructor Brandon | Dynatuners, we always seek innovative methods to improve your competitiveness and suit your Microsoft Dynamics 365 requirements. Our offerings are founded on defined procedures, industry experience, and product understanding. If you’re interested in consulting with our technical solution on customization to link the marking parameter and functionality concerns for using Dynamics 365 Mark Orders, feel free to Contact Us and get more information on it.
[sc_fs_multi_faq headline-0=”h2″ question-0=”What is d365 FIFO? ” answer-0=”First in, first-out (FIFO) is an inventory management and valuation system in which inventory is sold, utilized, or disposed of in the order in which it was produced or obtained. You can get pass the FIFO principle by labeling inventory transactions so that a single item receipt is settled against a specific issue. ” image-0=”” headline-1=”h2″ question-1=”What is BOM calculation? ” answer-1=”Bills of material (BOM) computations use data from various sources to determine a manufactured item’s typical costs. The sources are information regarding items, bill routings, indirect cost calculation algorithms, and the costing version. ” image-1=”” headline-2=”h2″ question-2=”What is pegged supply? ” answer-2=”Pegging is the process of recognizing connections between supply chain processes. As a result, we may link product inventories and production orders to client orders. Alternatively, stocks and production orders of semi-finished components might be linked to product production orders. ” image-2=”” count=”3″ html=”true” css_class=””]