Optimize Vendor Operations through Scheduled Subcontracting
Scheduled Subcontracting | Vendor Operations | Dynamics 365
Congratulations! Your company just received a new big project, and now the fun begins with project managing and purchasing. Effortlessly, you just need to pull on a bit of recap and start creating purchase orders and subcontracts; sounds easy, right? But what if the new big project has strict requirements against the scheduling of vendor operations?
Have you ever dread tracking the vendor operation requirements? Who submitted them? Is there any missing information? Are all vendor operations optimized regarding the scheduling? Or do you know if your vendors are qualified for SBA reporting, particularly when you are required to provide reports quarterly to the project owner? How would you know if the special requirement on the project is covered and approved by the vendors or subcontractors?
Dynamics 365 vendor operations simplify and enable a systematic way to keep track of subcontracted processes. With such automation, you don’t need to track vendor operations manually.
In today’s post, we will elaborate our readers on how they can optimize operations through scheduled subcontracting in Dynamics 365 and what improvement such automation can bring to your industry.
Production Subcontracts in Dynamics 365
There are several subcontracted production scenarios, and different ERP systems offer different modeling methodologies for subcontracted manufacturing. Microsoft Dynamics 365 even supports a variety of methods, such as the variations between efficient production and Kanban orders.
The various situations in subcontracted production often reflect differences in provided material and completed quantity handling and how these are represented and reported in D365. It’s best to describe these differences by starting with a simple model of manufacturing order processing for subcontracted production. All crucial factors are the visibility of inventory at the subcontractor site, those in transit, the dual structures of a production order, and its linked purchase order for the subcontracted service.
Variations in Subcontracted Production
There are several possible scenarios of subcontracted production. Each scenario reflects variations of the following factors
- Routing information with external operations.
- The Supplying of materials.
- Handling of finished quantities.
- Modeling of inventory locations in subcontracted production.
All of these factors offer an organized focus for other clarifications. The primary issue concerns the perceptibility of vendor managed inventory at the site of the subcontractor and in-transit stock.
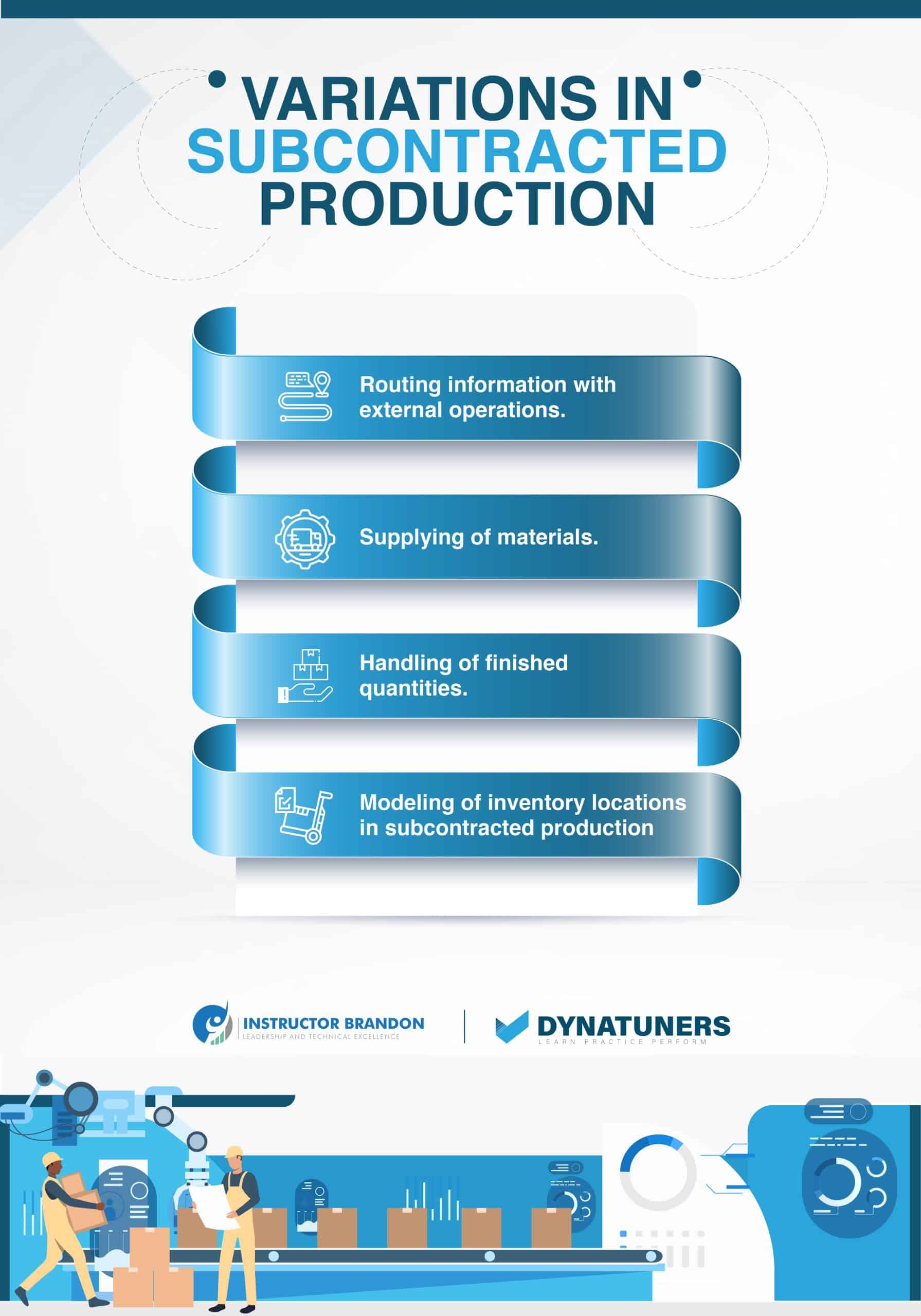
SUMMARY
Several studies demonstrate the differences in subcontracted production. The need for routing data, reporting subcontracted production with additional receipt purchases, various subcontractors building the same item, purchases delivered to a subcontractor warehouse, sales order shipping from a subcontractor warehouse, and BOM components provided by the subcontractor are among them.
BOM Information for Subcontracted Data
One line item for the subcontracted service item appears on the BOM version for a subcontractor’s manufactured item, whereas other line items identify the provided components. For subcontracted production, the standard business process for defining bills of material template information is the same as internally manufactured items. However, there are a few points that deserve special attention.
Defining BOM Policies
The BOM versions are usually site-specific to make it easier for the user to clearly identify the warehouse source of components supplied in the BOM line. This sort of site-specific BOM is helping when different subcontractors produce the same product.
Defining BOM line for Subcontracted Service
The BOM line indicates a buy-to-order service by defining the subcontracted service item and a line type of vendor. Typically, only one quantity is required. You must also mention the corresponding operation number and mark the line as due at the end of the operation when using routing data. The due date for the item’s purchase order will be aligned with the due date for the linked production schedule.
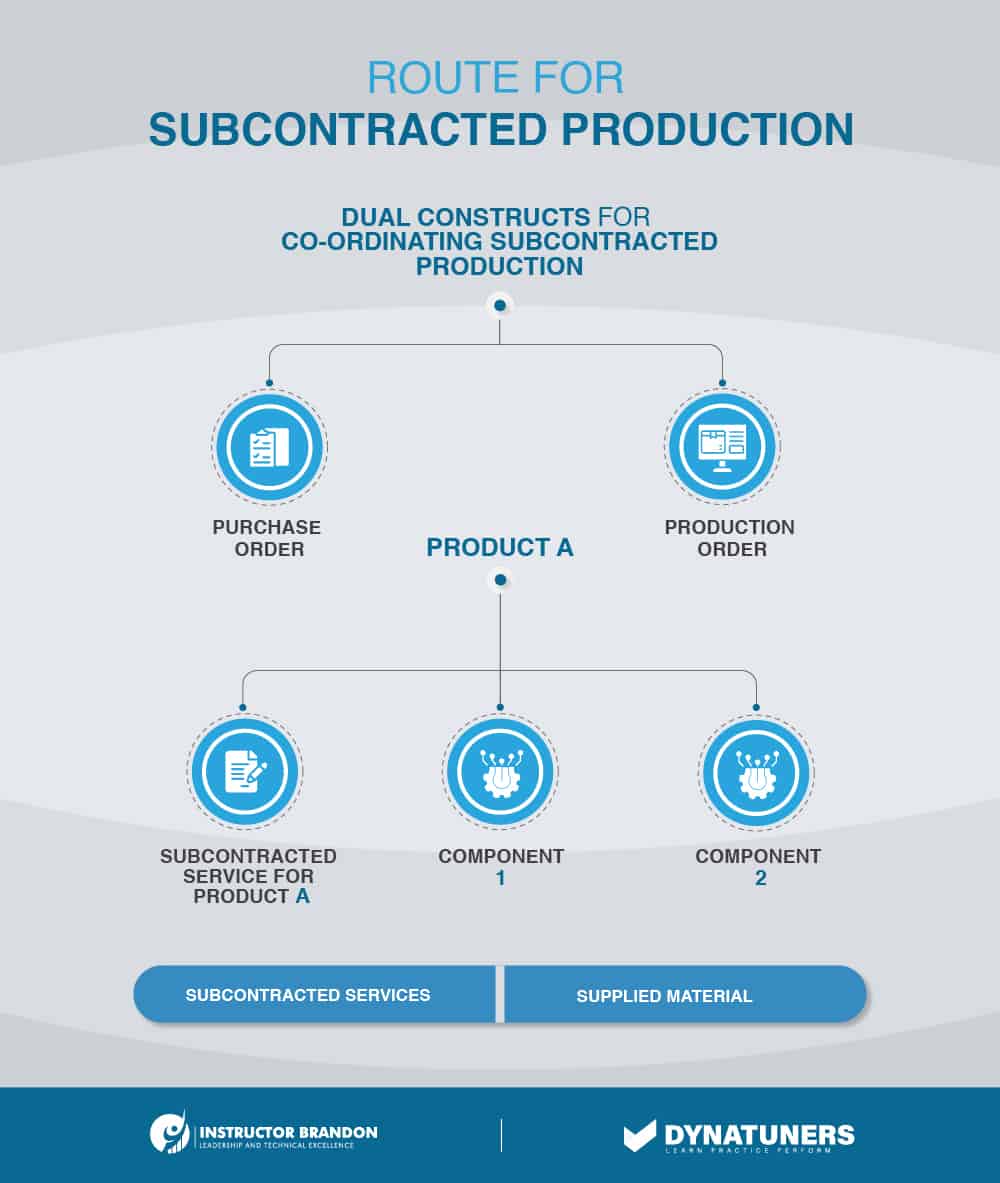
Define BOM line for Supplied Components
Each provided component and its needed quantity are defined on a separate BOM line. The warehouse source of ingredients is usually given as part of the bills of material example line, although it can also represent one of the other warehouse source alternatives. The flushing policy for the component and the appropriate choice should describe the required variation of supplied components.
In some cases, the material provided by the subcontractor is also identified.
SUMMARY
Internal production and subcontracted production have a lot in common. However, several subcontracted production scenarios involve significant differences in inventory tracking and supply chain transparency via the dual structures of a production order. While a relating purchase order for the subcontracted offering via the dual constructs of a production line and a correlating purchase order for the outsourcing service.
The above heading covered the significant differences in provided material and final quantities and crucial contract workers’ production components such as service items, BOMs, and routings.
On the Job with Activity-based Subcontracting
Microsoft Dynamics 365 focuses on two methods when it comes to subcontracting. The first one is lean manufacturing, and the second is called production orders. The lean manufacturing approach is subcontracting work as services linked to an activity-based production flow. Further, the user is introduced with a direct outsourcing cost group type, and subcontracting services become independent from bills of materials. The cost solution for lean manufacturing processes integrates with cost accounting of subcontracted work.
Subcontracting of Production Flow activities
The primary goal of production flow stays the same when activities are assigned to subcontractors. The material for production still flows in the same way between different locations. Activities convert the material into products, and activities for a transfer move products or material from one place to another. As the vendor manages the vendor accounts to a warehouse or resources to resources group, Dynamics 365 allows you to model locations and work cells accordingly.
Based on such capabilities, you don’t need to put in specific features to lean manufacturing principles supporting the flow of products or materials. You can model them based on the roadmap or architecture of the activities and production flow in any scenario where a vendor or transport services are involved.
For instance, a subcontractor deals out the market located at the subcontractor. While handling units become vacant from the subcontractor’s end, the assembly cell gets its Kanban cards returned with the details about the next shipment. The market at the subcontractor or the vendor, receives the status of replenishment. All the transfers from or to the subcontractor then models as “direct transfer activates” to support shipment and picking processes. However, if there isn’t any requirement for explicit registration to keep the actual transport, Dynamics 365 can omit transfer activities.
You can use subcontractors to load balance in the overall capacity of the production flow. For instance, you can model a production flow by using the schedules Kanban example rule. The planner makes use of the Kanban system scheduling board to both load and schedule work cells on demand. The planner, further monitors the compressed schedule for the market that you can see on the supply schedule page. Users in Dynamics 365 can also model subcontractors in single or multiple production flows. Whereas, there could be numerous Kanban rules to supply the same product to the exact location with the help of different activities.
The planner can reschedule a Kanban initially established for internal production to an alternative process by converting it to an alternative Kanban methodology. For two parallel internal work cells or two subcontracted cells, the same operating concept applies.
Like all the other activities in the production flow, subcontracted activates can devour and supply all sorts of materials and products, including inventoried, non-inventoried, and semi-finished. For all of these cases, the process improvement for scheduling and implying subcontracted activates stays the same. Moreover, these processes are the same as the processes for internal workings.
While we are on to creating subcontracts for the production orders, we know that having all of them with accurate schedules.
Various Forms of Subcontracting |
|||
Variable | Weight | ||
Duration of activity of the subcontract | Short | Moderate | Long |
Place where the subcontract carries out work | External | Intermediate | Internal |
Share of activity in the organization | Small | Average | Significant |
Nature of subcontracting activity | Simple and
substitutable |
Average | Complex, non-substitutable |
Place of the subcontractor in the process | Supply | Intermediate Production | Final Production |
SUMMARY
In lean manufacturing, activity-based subcontracting allows you to integrate carriers and transport suppliers who transfer materials and products between production flow points. You can attribute a carrier or vendor to a transfer operation by modeling it. The transfer activities/job is based on a service and purchase agreement, and you can use the actual transfer jobs to make purchase orders and receipt advisories. This is the same functionality as the functionality for subcontracted process activities.
Create and schedule Kanbans for subcontracting
Before we create Kanbans for subcontracting from kanban tool, we need to set up a few prerequisites to ensure a smooth subcontracting process.
Step 1
Set up a default vendor for a warehouse.
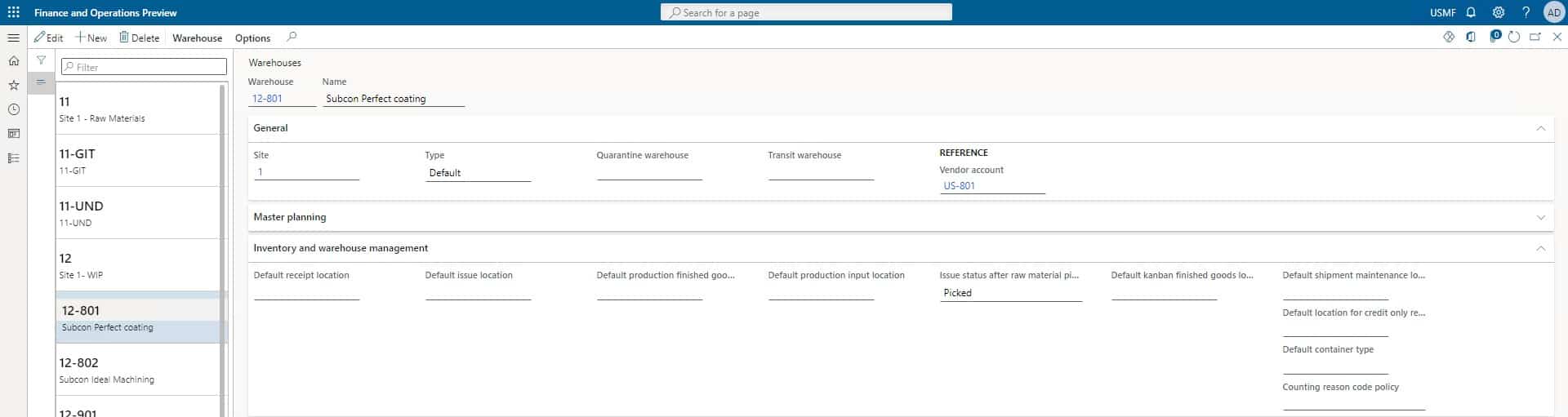
Step 2
Create a purchase agreement.

Step 3
Create a work cell for subcontracting.
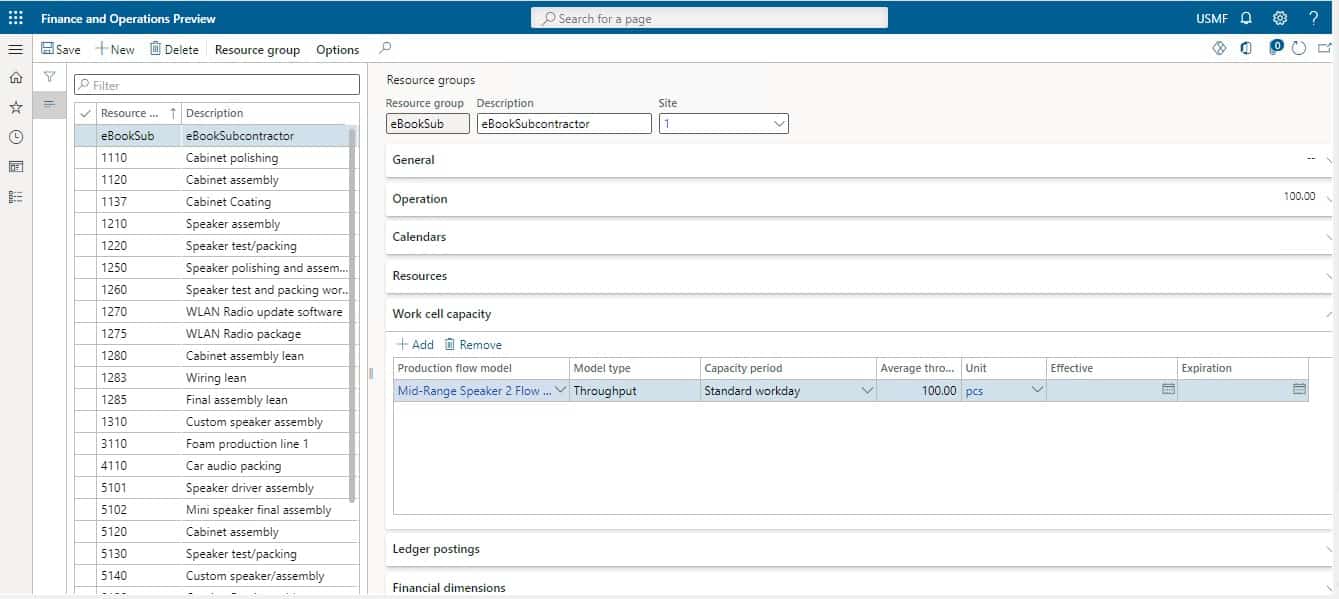
Step 4
Create an activity-based subcontracting rule.
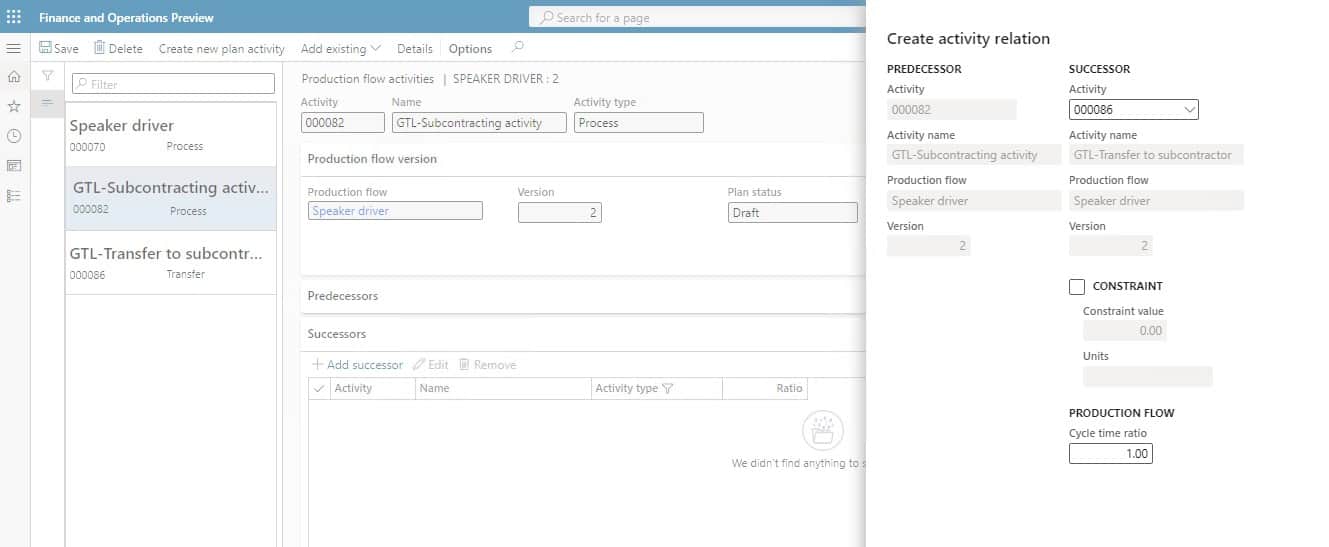
Once all these prerequisites are fulfilled you can continue with scheduling kanbans for subcontracting.
Create and schedule kanbans for subcontracting:
First, we need to set up unit conversion in the demo data to be able to perform this.
Step 1
Go to Product information management > Products > Released products.
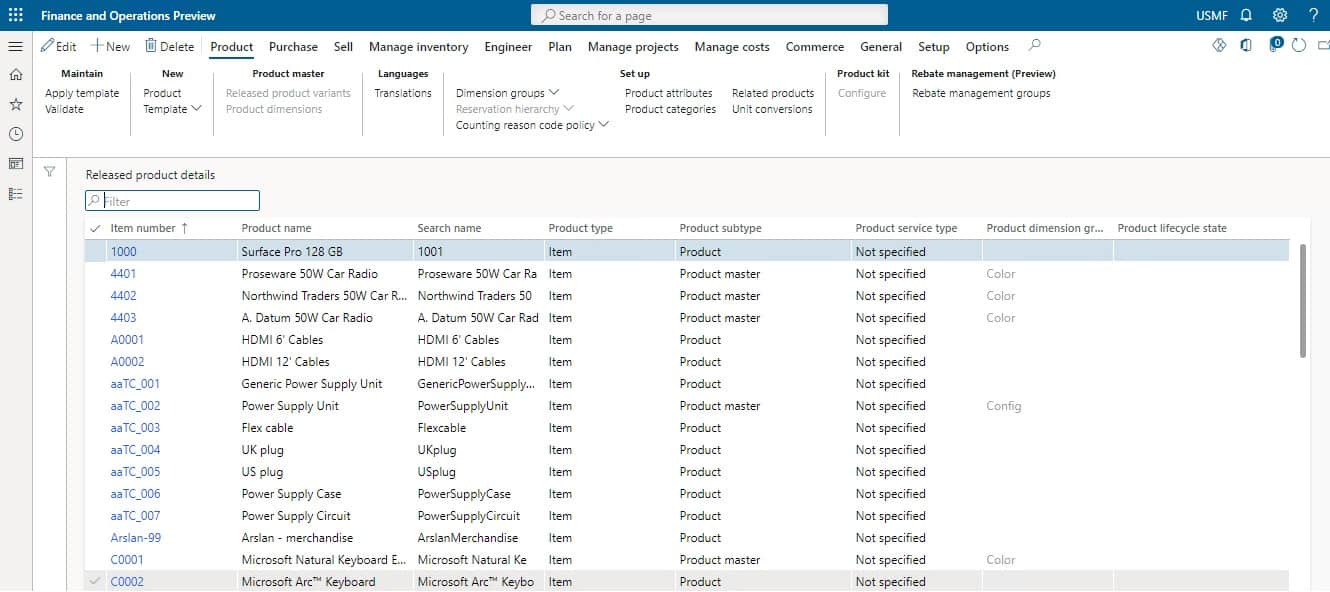
Step 2
Select the product L0001.
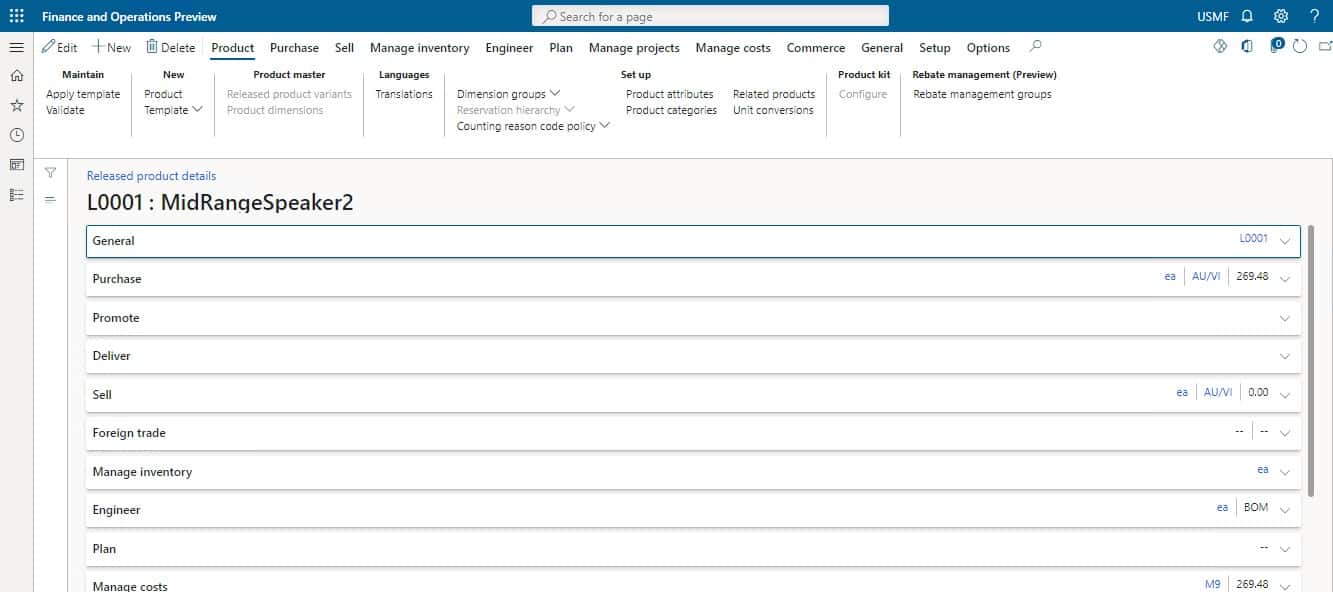
Step 3
On the Product Fast Tab, select Unit conversions from the Set up group.
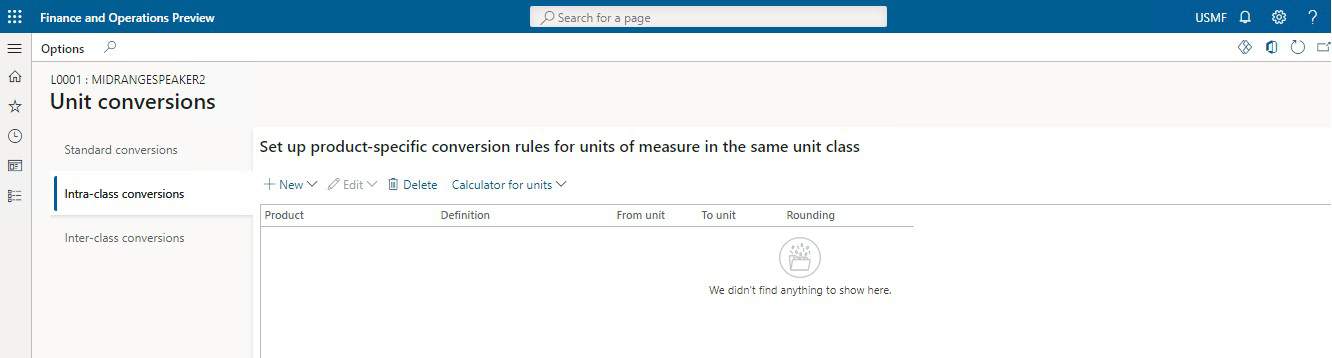
Step 4
Click on Inter-class conversion and select new.
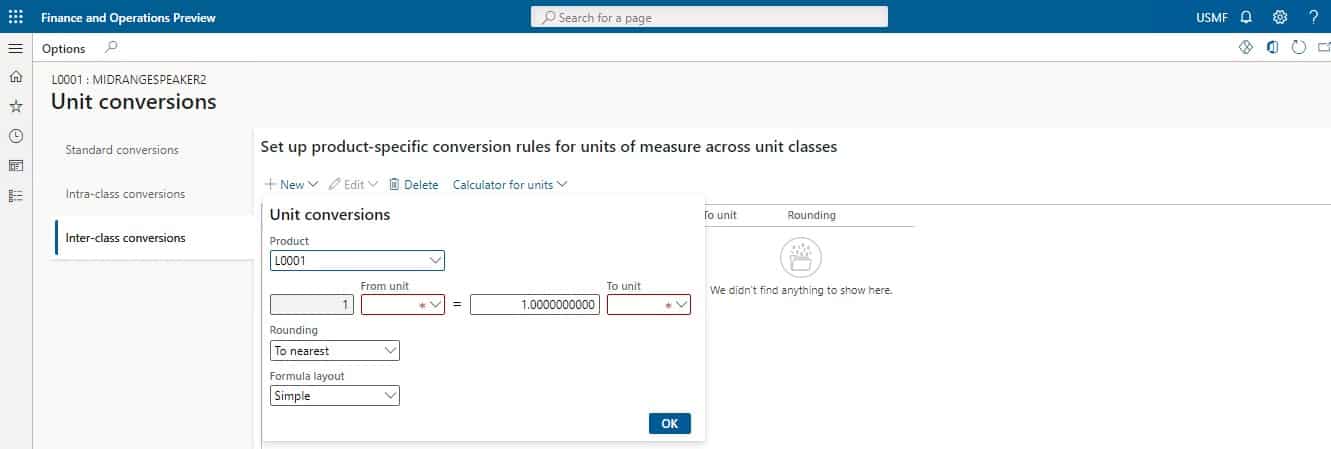
Step 5
In the From unit, select hr; in the To unit, select ea. Select OK and close the page.
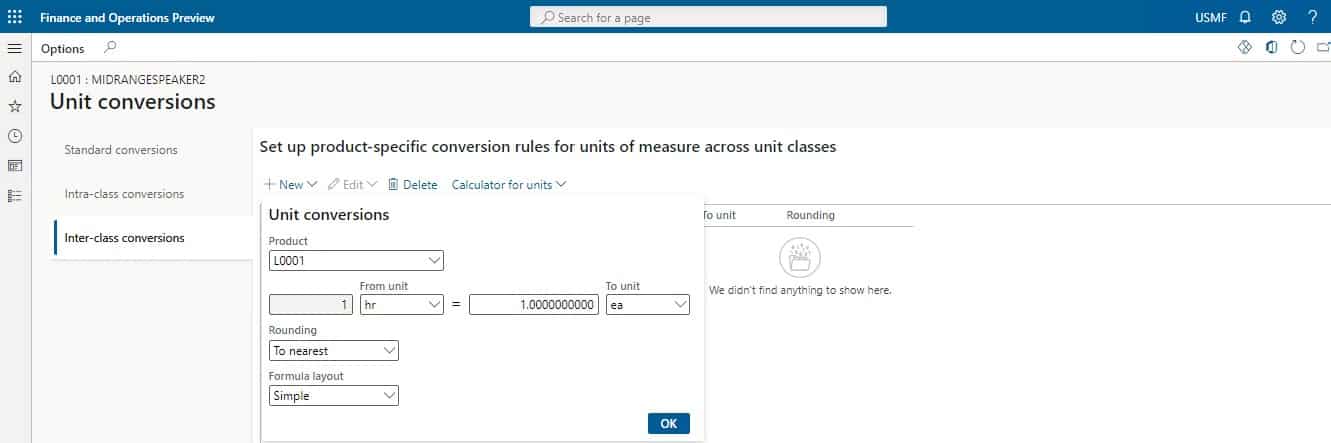
Step 6
Go to Product information management > Lean manufacturing > Kanban rules.
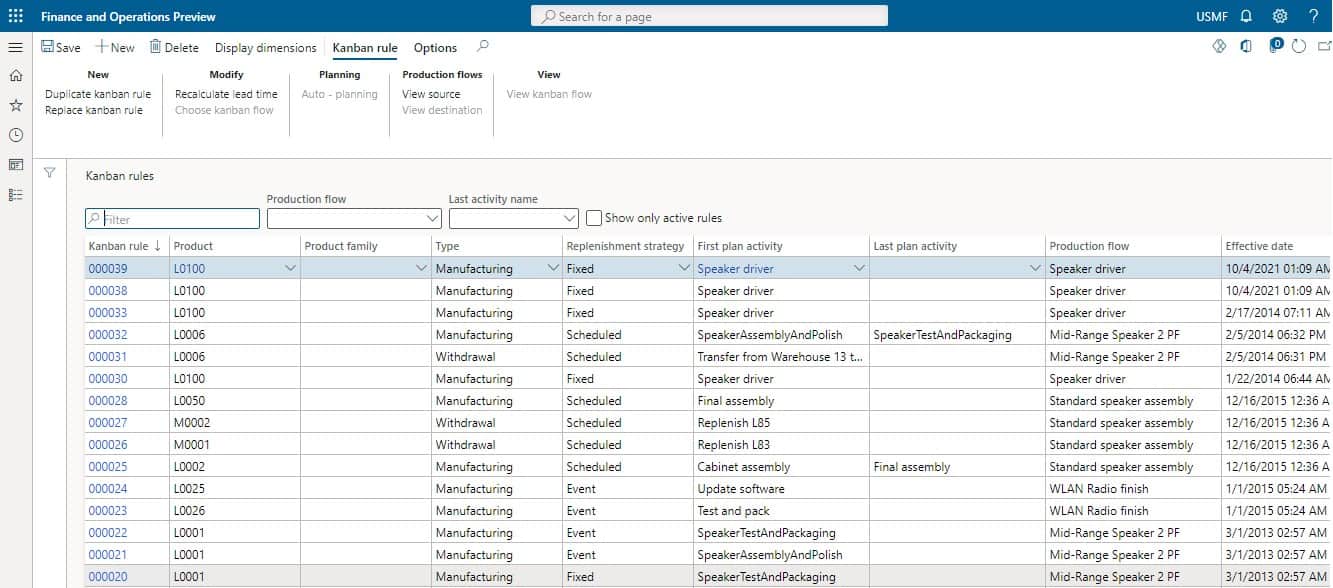
Step 7
Click on New. In the First plan activity field, select GTL-Subcontracting activity. Select the Multiple activities check box. In the Last plan activity field, enter or select GTL–Transfer to subcontractor. On the Choose Kanban flow page, select Generate flows. Select OK.
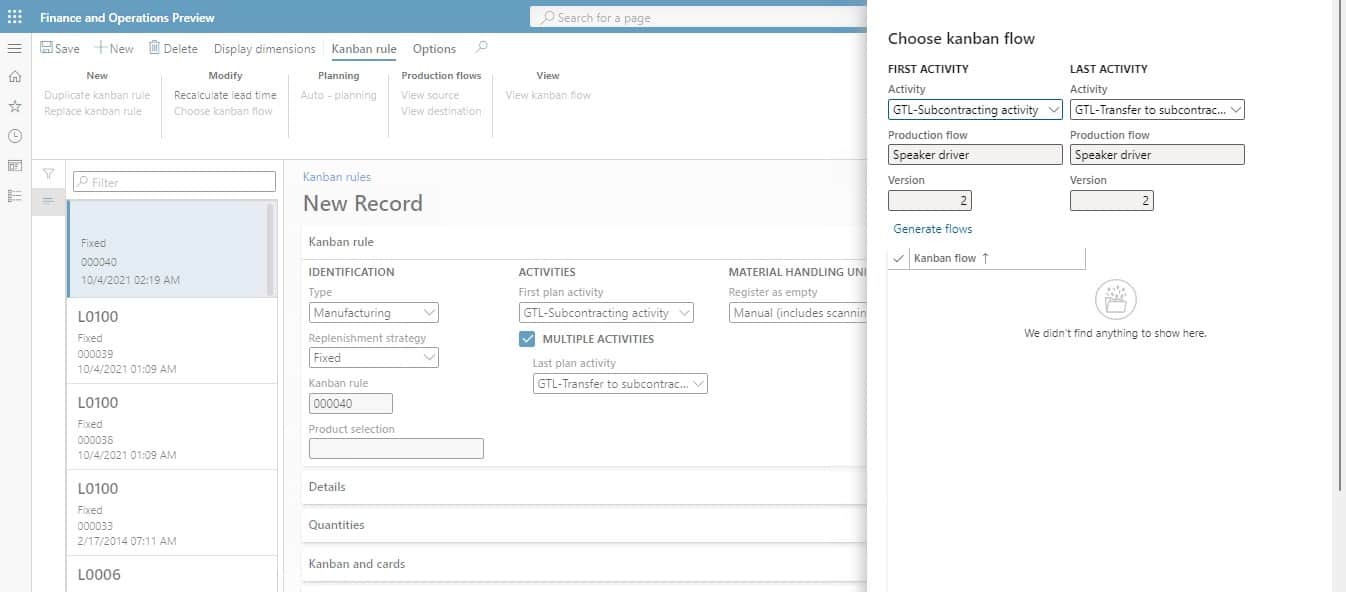
Step 8
On the details fast tab, select L0001 In the product field.
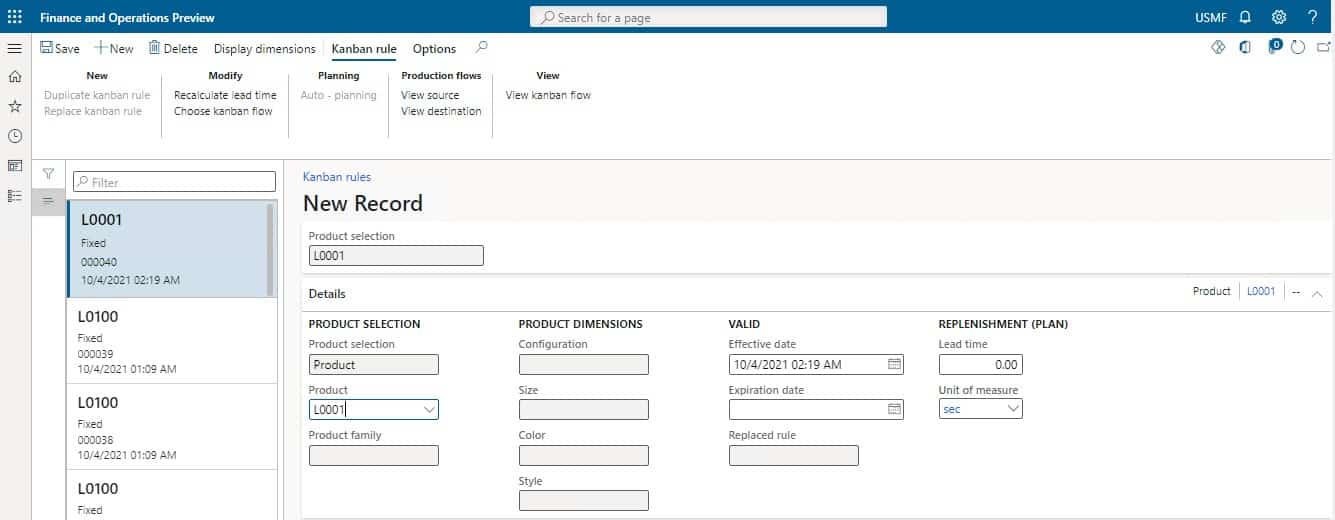
Step 9
Expand the Quantities section. Set Default quantity to 50.00. In the Fixed kanban quantity field, enter 25. Select Save.
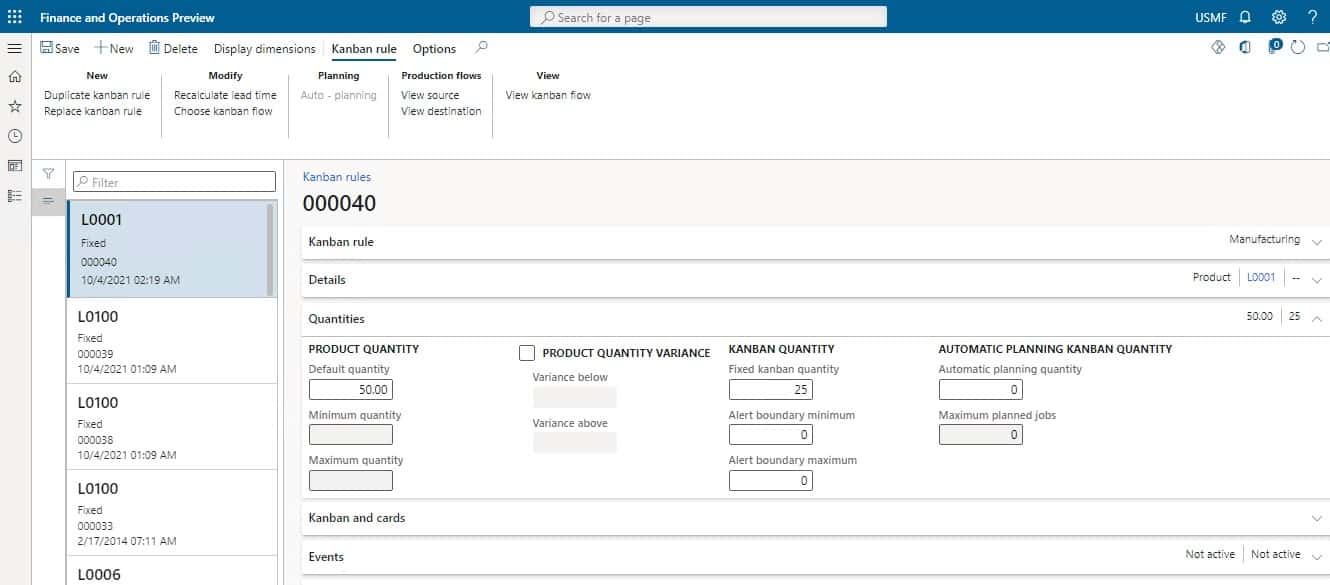
Step 10
Expand the Kanbans FastTab. Select Add. In the Number of new kanbans field, enter 1. Select Create.
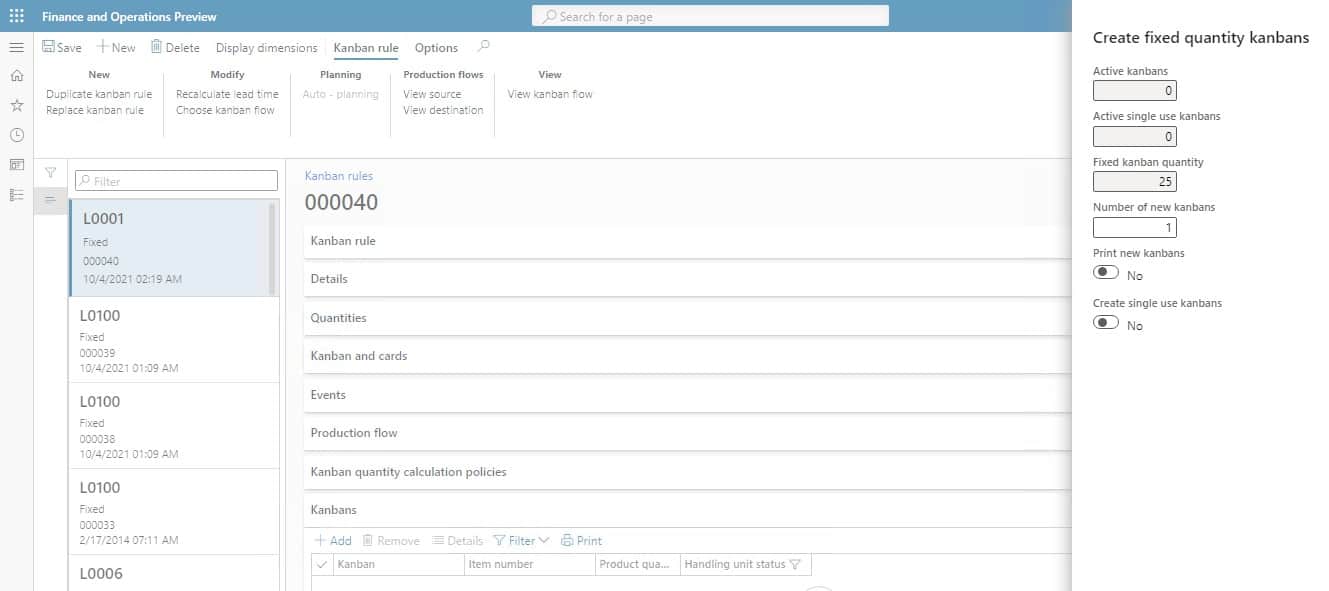
Step 11
Select Details. Expand the Jobs section. View jobs for process and transfer to a subcontractor and then close all pages.
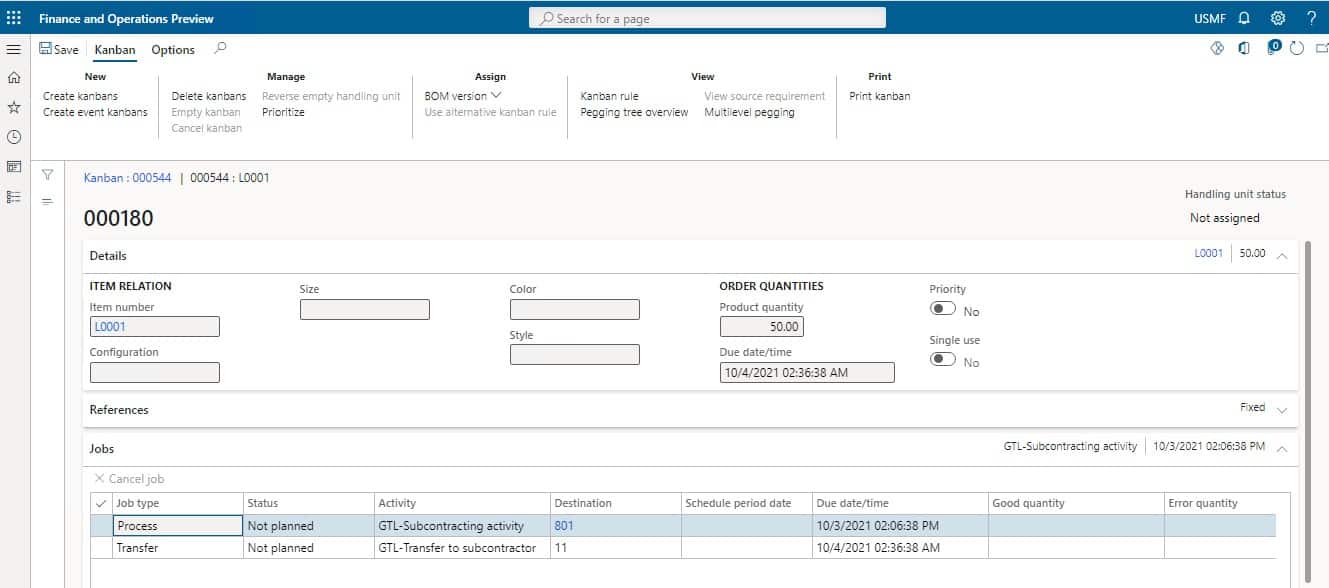
Step 12
Go to Production control > Kanban > Kanban job scheduling
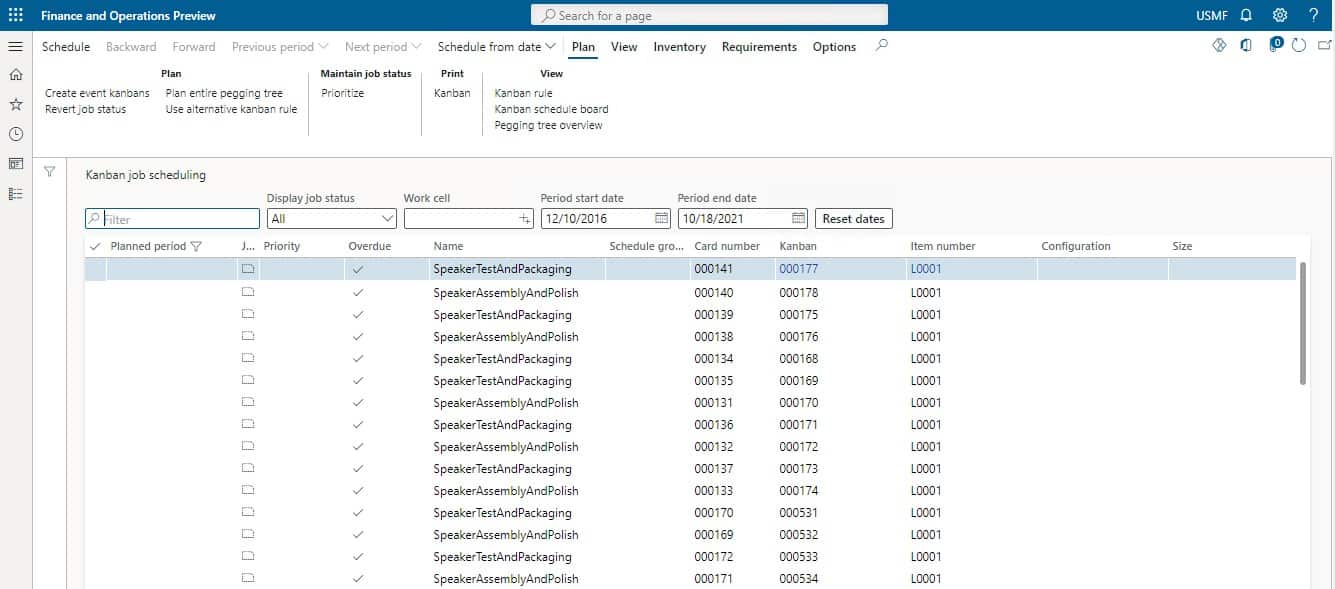
Step 13
In the Work cell field, select eBookSub. In the list, select the first row. Select schedule from date to open the drop-down dialog box. Select schedule and close all pages.
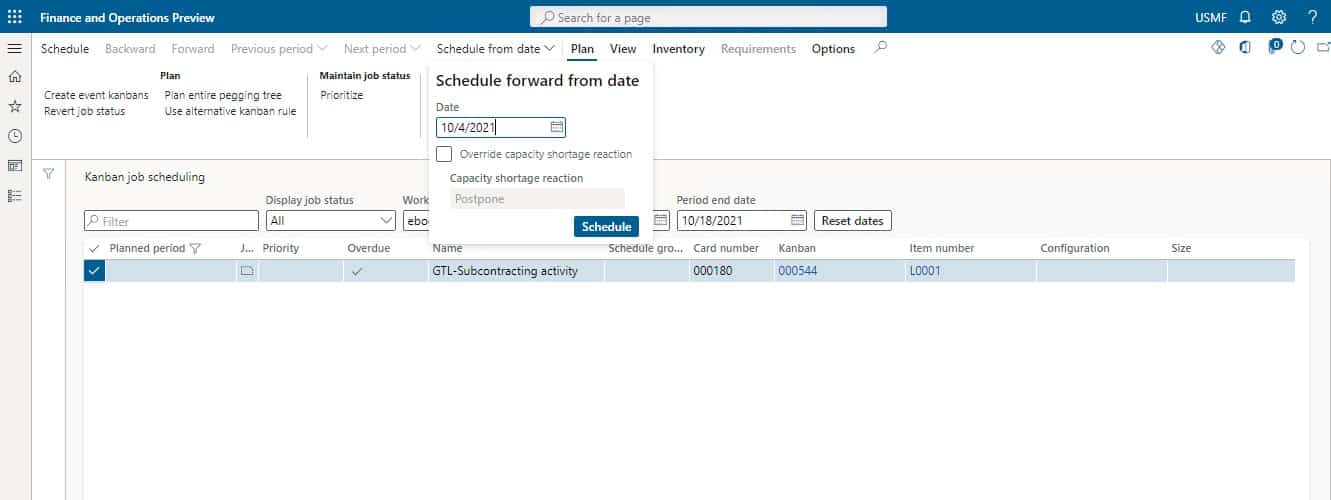
SUMMARY
By following this step-by-step guide users can create Kanban job subcontracting for vendor operations.
Why should you go for scheduled subcontracting?
There is a priority for scheduling in every project. The scheduled contracting or subcontracting defines how quickly the task will be completed and how it will be completed. The scheduled subcontracting specifies the order in which the materials will be installed and the method by which they will be installed, as we have discussed above in detail. As a result, the sooner the schedule is available to the project team, the better.
The scheduler must consider controlled products while keeping the design’s integrity. To build a proper scheduled subcontracting, the scheduler must comprehend the projected scope of work as well as the details affecting the connection of each component.
The project manager can analyze multiple different installation sequences to arrive at the most productive arrangement by understanding the actual lead times, cost management, and how supplies will be assembled. Avoiding last-minute surprises or a lack of forethought can save project money and time by avoiding high costs and delays.
Here are some advantages to scheduled subcontracting in Dynamics 365.
- The necessity to plan ahead of time allows for a better understanding of the specifics and fewer surprises later on in the project.
- By appropriately sequencing the job, you may maximize quality control measures.
- It improves resource planning, such as workforce and equipment.
- You will also witness improvement in coordination efforts between the client and construction activities.
- Purchasing supplies and crucial components with sufficient lead time.
- Schedule subcontracting will also incorporate timely submission of shop drawings, samples, and datasheets.
- Subcontracting on time will affect the time for others, such as subcontractors, vendor management, designers, and clients, to properly organize their own activities.
- Schedule subcontracting will improve safety performance by sequencing actions to ensure that workers are protected to the fullest extent possible.
- Schedule subcontracting will reduce the danger of damage to nearby property and completed work, resulting in a shorter punch list.
- Knowing which weather-sensitive activities will be put in place during cold weather, as well as the duration of such activities, will help you price winter protection measures appropriately.
- Schedule subcontracting will increase production to the maximum level possible to accomplish the job in the quickest timeframe achievable.
According to a study, there is a positive, quantitative association between the work put during the pre-project planning phase and the project’s eventual success.
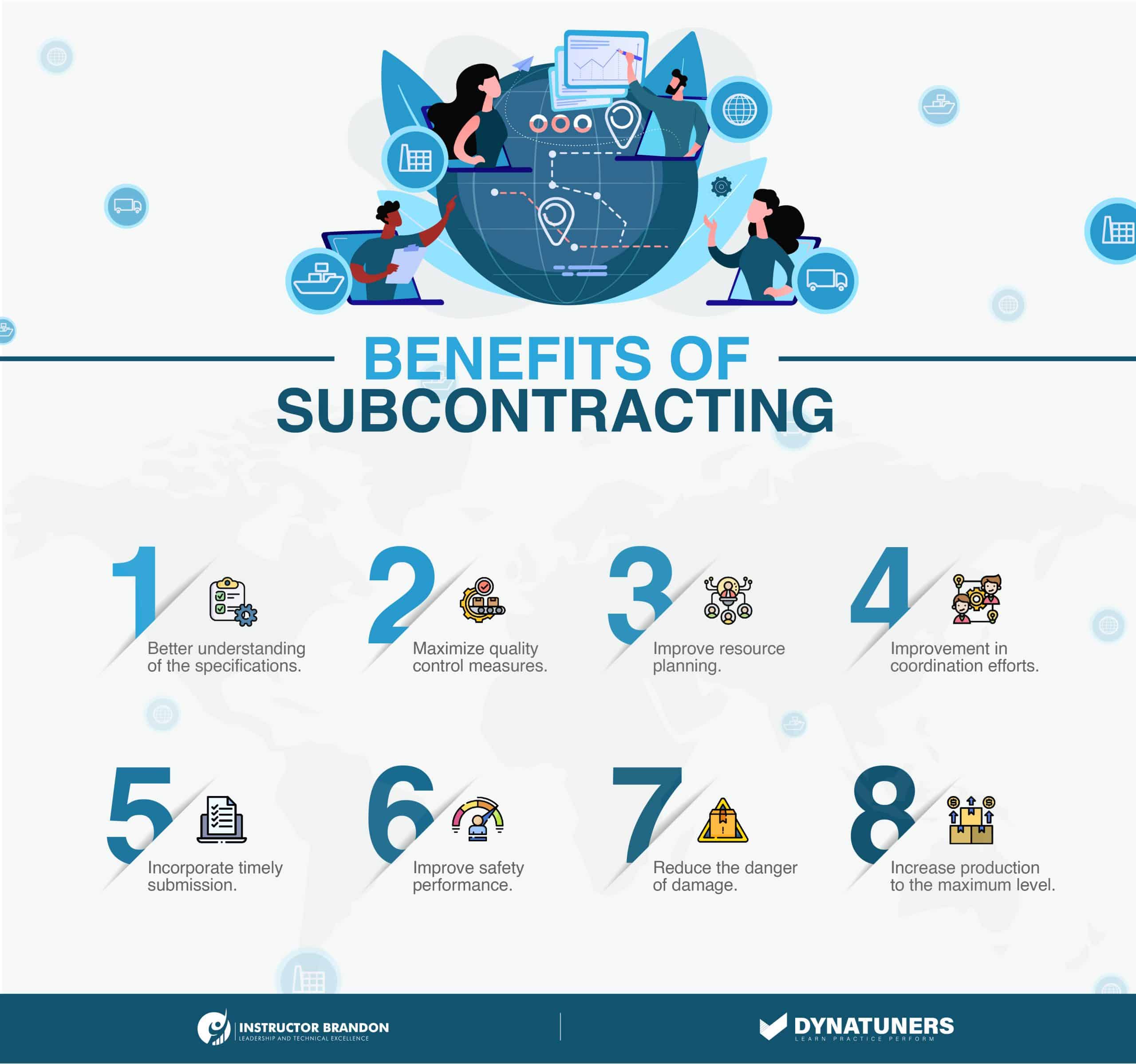
SUMMARY
The importance of adequate planning cannot be overstated. Every venture requires proper planning and the hard work necessary to put the strategy into action. Well-planned scheduling will help all team members in numerous ways, and we all should make preparations for a successful project.
At Instructor Brandon | Dynatuners, we always seek innovative methods to improve your competitiveness and suit your Microsoft Dynamics 365 requirements. Our offerings are founded on defined procedures, industry experience, and product understanding. If you’re interested in consulting with our specialists on how we can help you optimize your vendor operations by creating and scheduling Kanban for hustle-free subcontracting, don’t hesitate to Contact Us.
[sc_fs_multi_faq headline-0=”h2″ question-0=”What processes involve subcontracting? ” answer-0=”Raw materials are delivered to the subcontracting vendor during the subcontracting process. It’s being processed by a subcontractor, who will then convert it to semi-finished material and return it to you. Multiple subcontractors are frequently utilized for production at various levels of the BOM. ” image-0=”” headline-1=”h2″ question-1=”How do you calculate subcontracting costs? ” answer-1=”The expenses of subcontracting are calculated based on the gross input of the finished goods. The expenses are determined by multiplying the subcontracting rate factor and the subcontracting rate by the end item quantity presented in the Ordered Quantity field of the Purchase Order Lines (tdpur4101m000) session. ” image-1=”” headline-2=”h2″ question-2=”Are there any downsides of subcontracting?” answer-2=”Contractors/subcontractors may end up costing your company more than hiring someone full-time…. Contractors may detest being paid more money for doing same work to your own employees. ” image-2=”” count=”3″ html=”true” css_class=””]