Cost Distribution Policy in Microsoft Dynamics 365
Cost Distribution | Distribution Policy | Cost Control Unit
Recording, examining, understanding and summarizing the flow of cost spent on your business processes, services, or products can help you control and engage in strategic ways to refine and improve cost efficiency. Thus, the way you manage cost control becomes a pillar of your business foundation.
Seemingly, the objective of cost controlling is to identify and reduce business expenses and gain higher profit margins. However, in pursuit of seeking continuity and presence in the market, you need to build a robust system of cost proportioning based on your business activities. Moreover, providing accurate information of production cost can allow you to have a firm grip over the cost elements while excluding avoidable costs and finally reducing product cost as much as possible.
With such cost driver reduction, you provide your customers with more affordable products and increase sales and profits eventually.
Among the above, there are many other distribution factors of accounting; therefore, allocation and distribution of cost play their respective parts in driving cost. Once your collective cost center is allocated financially, you can set cost distribution rules for it. The cost accountant will ensure that the cost is distributed appropriately according to the plan.
The core for our today’s topic will make our readers aware of setting rules for cost distribution in Dynamics and how it works. However, before getting into the process of setting rules, let’s first go through a couple of insights to cost accounting that may help you get a better idea of the working of cost distribution rules on Dynamics 365.
What is Cost Control?
There are two major concerns at the heart of cost control: First, who can spend the money? Second, on what he can spend the money?
For this, we should have a clear understanding of what type of expenditures are suitable for the company. However, cost control in a cloud-based world comes down to, permission to spend money by consuming resources. Cloud computing has ways to handle holding costs by defining control policies to the native system and pointing out which roles can provide resources under certain conditions.
All in all, the purpose of cost control is to provide your firm with a solid foundation for improving visibility and keeping expenses under control.
The Role of Dynamics 365 in Cost Controlling
It’s no secret that cost comparison and management require a lot of data and analysis. Therefore, it’s no wonder that Dynamics 365 have discovered a use for automation in these areas. In a variety of ways, Dynamics 365 Finance can help you improve the following process:
- Through Dynamics 365, tedious computations and other quantitative chores become practically instantaneous and impervious to human mistakes.
- The analysis becomes considerably more manageable when data is displayed through dashboards and easy-to-use user interfaces.
- This method allows for automated data standardization, which is beneficial for worldwide projects that need the usage of several currencies.
- Third-party interfaces with other management systems aid in the more efficient pooling of data.
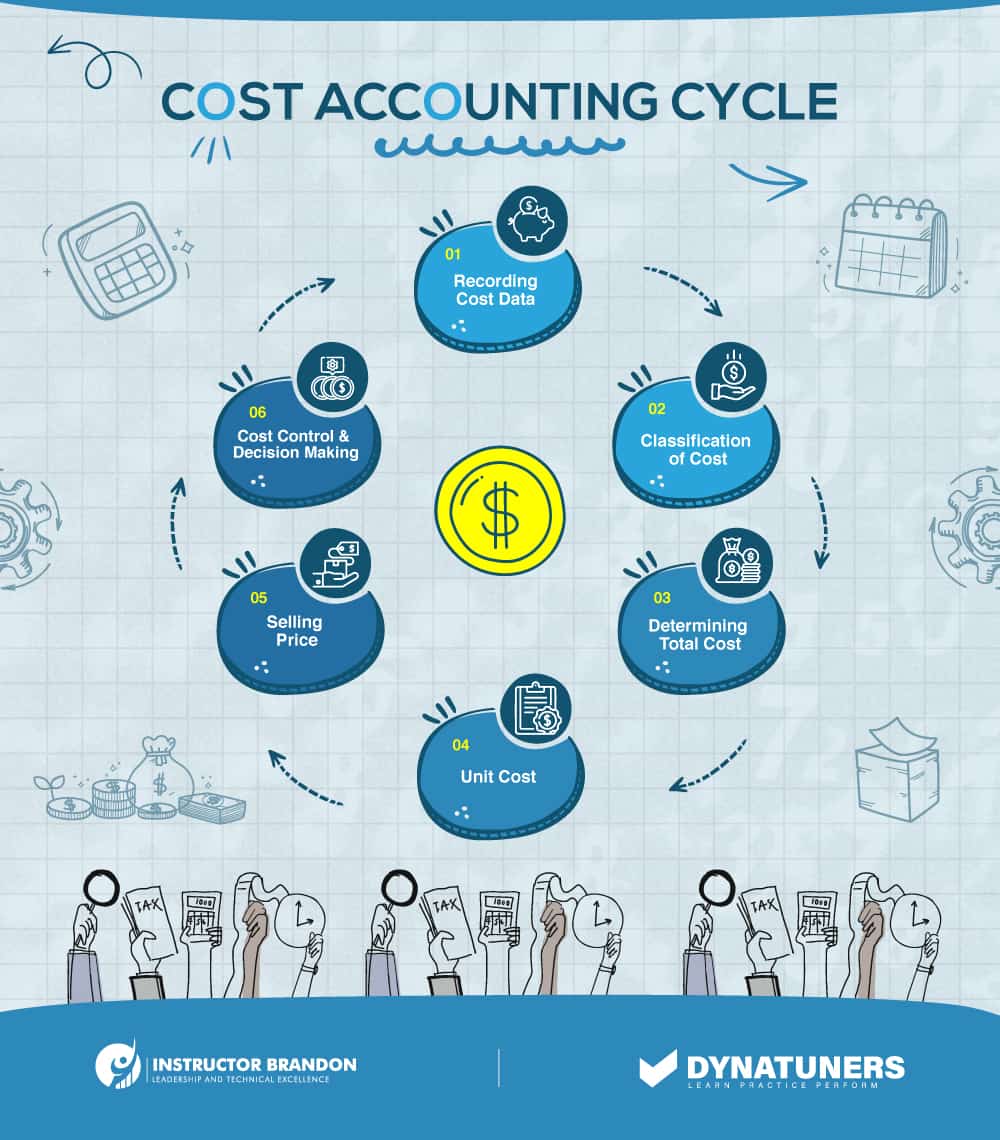
SUMMARY
Identifying and cutting corporate expenditures to maximize profits is called cost controlling, and it starts with a budgeting process. Your company’s actual financial outcomes are compared to budgeted expectations, and if actual expenses are higher than predicted, management should have the knowledge it needs to take action.
Process Steps for Cost Control
Grasping to business expenses is certainly not about just setting them and forgetting about them. Instead, it is more like making contentious amendments to cyclical processes. So, to give our readers a better idea of how cost controlling works on a deeper level. Here are the process steps on which cost control is based:
Organizing Resources
Implementing project controls is the first step in cost management, anticipating the future expenses of a project is crucial, whether it’s for equipment, materials, personnel, or even just time spent. Before the actual job begins, the resource planning process is completed.
The work-breakdown structure is frequently used by businesses to review subtasks in the schedule while determining what skills or equipment are required for each. Financial reporting data from similar projects in the past and comments from team members are critical factors to consider for this work.
Here are a few pointers to keep in mind as you go through the process:
- Before selecting sub-tasks and accompanying resources, consider historical data—past timelines and effort.
- Take input from SMEs and team members – a collaborative approach is ideal for initiatives that lack historical data.
- Examine how time affects resource requirements. For example, a resource may not be accessible for several months, causing the project’s timetable to be pushed back. This might affect budgeting.
- Even though this phase occurs during the planning stage, project managers must consider the reality on the ground.
Cost Estimation
Next, estimate the total cost of the resources required for the project. Cost estimating is a difficult task that is dependent on your current budget and the amount of information you have. Later, we’ll go through cost estimation in further detail.
Creating a budget
After the job has begun, the next step is to assign a budget to each activity. Cost budgeting is the process of combining predicted costs with the project schedule. Here, each action in the process has its own cost allocation.
Cost Analysis
Finally, project management must address how to deal with budget adjustments. Cost control monitors the deviation between actual cost calculation and the set baseline cost, taking action as needed. This phase also necessitates a review of the acts’ actual outcomes.
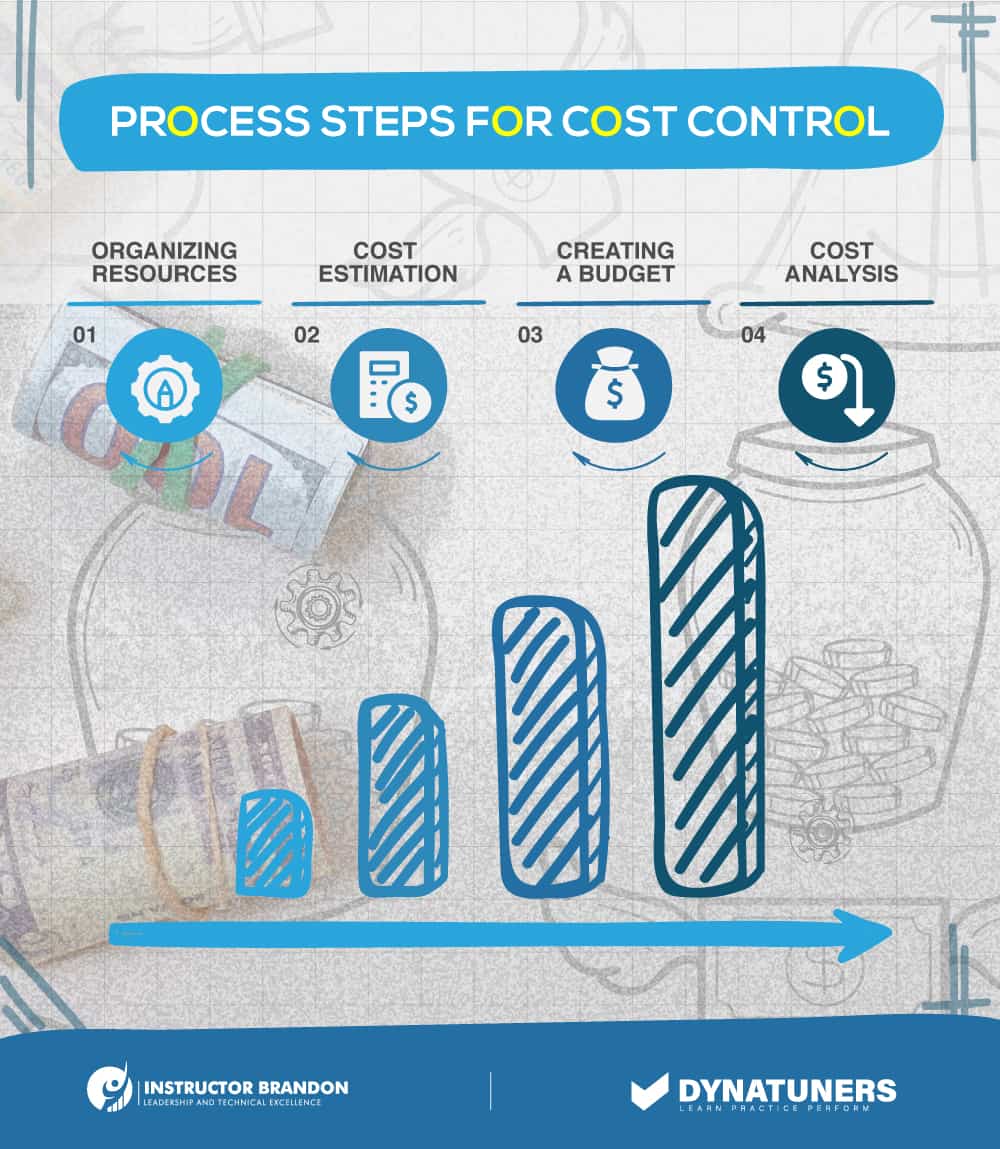
SUMMARY
Cost controlling isn’t just limited to the one-time role or a single-step process. Instead, cost control consists of several functions, and the above heading explains which steps a firm should go through to have a firm grasp over its expenses.
What Role Does Cost Distribution Play?
A firm’s cost distribution is an expense to make its services and goods available to the end consumer. In actuality, it is a broad financial accounting term, covering numerous aspects. For example, expenses for delivering goods to resellers and end-users, warehousing costs, transportation taxes and tolls, and vehicle upkeep are only a few instances of this cost.
Distribution cost can account for a significant portion of a company’s total costs, mainly when the commodities are perishable, the volume of goods is large, or the end-users are located in remote places.
The thing to remember here is that the elements of cost distribution don’t include the selling and marketing expenses. However, some preceding cost distribution policies came with shipping and logistic fees included in them. Whereas the selling and marketing expenses consisted of payrolls of marketing staff, the commissions for sales, and the advertisement cost.
What Distribution Cost includes?
As previously mentioned, it is a broad phrase that encompasses a wide range of expenditures. All costs associated with shipping the goods to end-users or resellers make up the distribution costs.
All shipping costs at each level (from the manufacturing plant to the reseller or end-user) are also part of distribution costs. For example, the manufacturer may have a production plant in one region and a pick-up site for the shipping agent in another. The cost of transporting items from the manufacturing site to the pick-up location will be included in the distribution costs.
Inventory cost handling at each shipping stage is also a part of the distribution costs. It will comprise handling fees at the manufacturing plant, the pick-up location, the warehouse, and the point of sale.
Packaging costs and administrative distribution charges may also be the distribution expenditures. Further, the pay of the distribution manager and the distribution manager’s office expenditures will also play their part as the administrative distribution cost.
Likewise, another crucial component of distribution cost is the freight expenses. While for some companies, it could also be trucking fees or so on.
All in all, we can conclude that the distribution cost consists of the shipping cost, packaging cost, freight expenses, storage cost, expenses for handling, and finally, the expenses for distribution of salary among employees.
Now that we have a pretty much idea of what cost distribution is and why companies need it, and what costs we can count as distribution ones, we can set off to defining its policies in Dynamics 365 Finance and Operations. However, the distribution policies vary from business to business depending on their specific cost distribution requirement across different divisions.
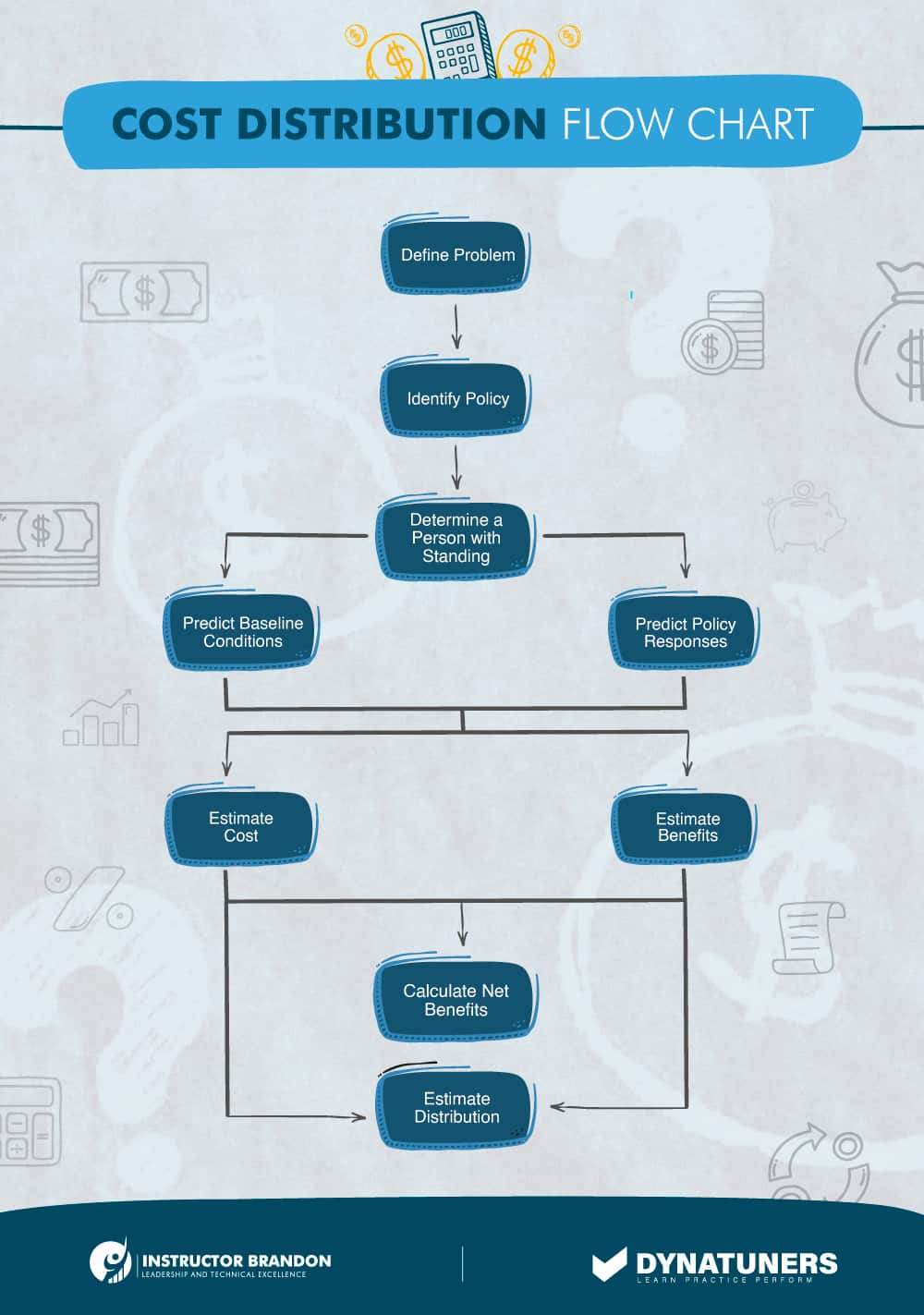
SUMMARY
Cost distribution plays a vital role in any firm. Above, there is a brief explanation of what is included in distribution cost and not. People at managerial posts can make an acceptable assumption on what sort of cost they reduce and which would benefit them most in reducing the price for their end product or service.
Create and Assign a Cost Distribution Policy to a Control Unit in Dynamics 365
Create a Policy:
Step 1
Go to Cost accounting > Policies > Cost distribution policies.
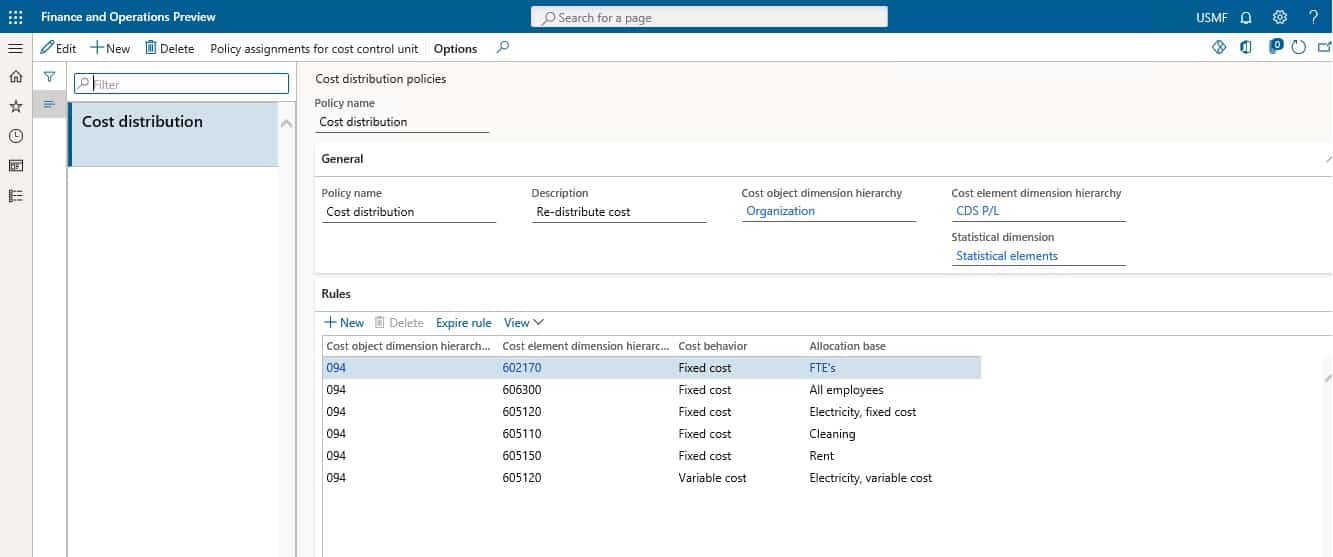
Step 2
Click New.
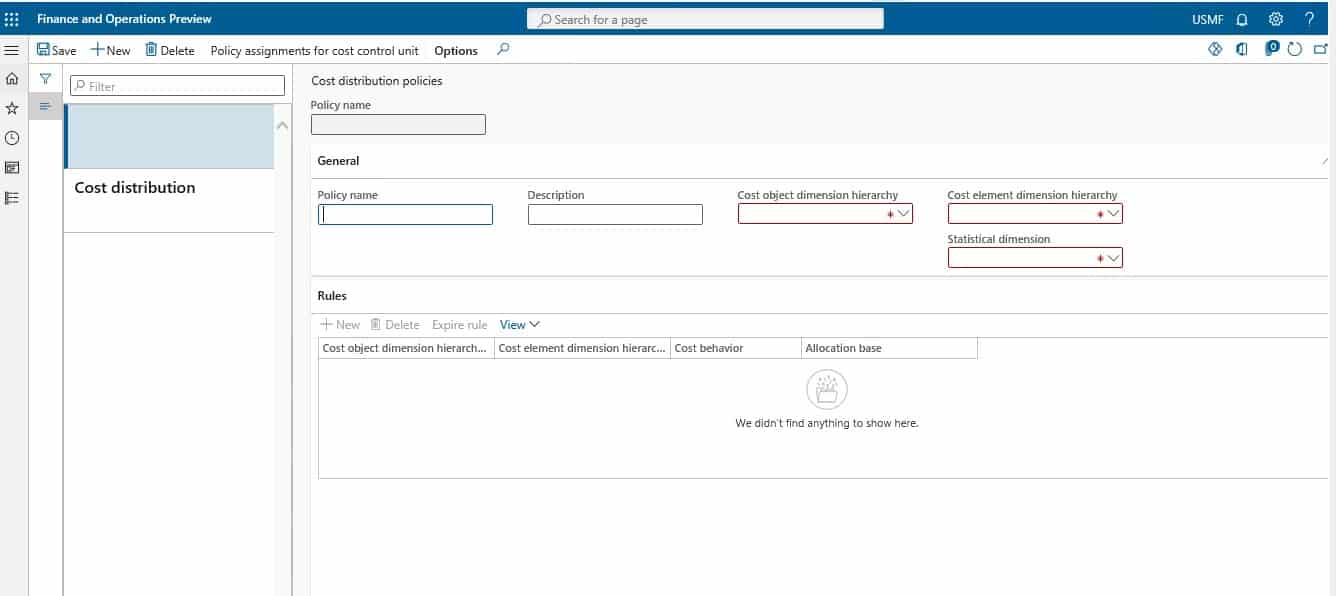
Step 3
In the Policy name field, type a value. In the Description field, type a value. In the Cost object dimension hierarchy field, enter or select a value. Select Organization. In the Cost element dimension hierarchy field, enter or select a value. Select CDS P/L. In the Statistical dimension field, enter or select a value. Select Statistical elements. Click Save.
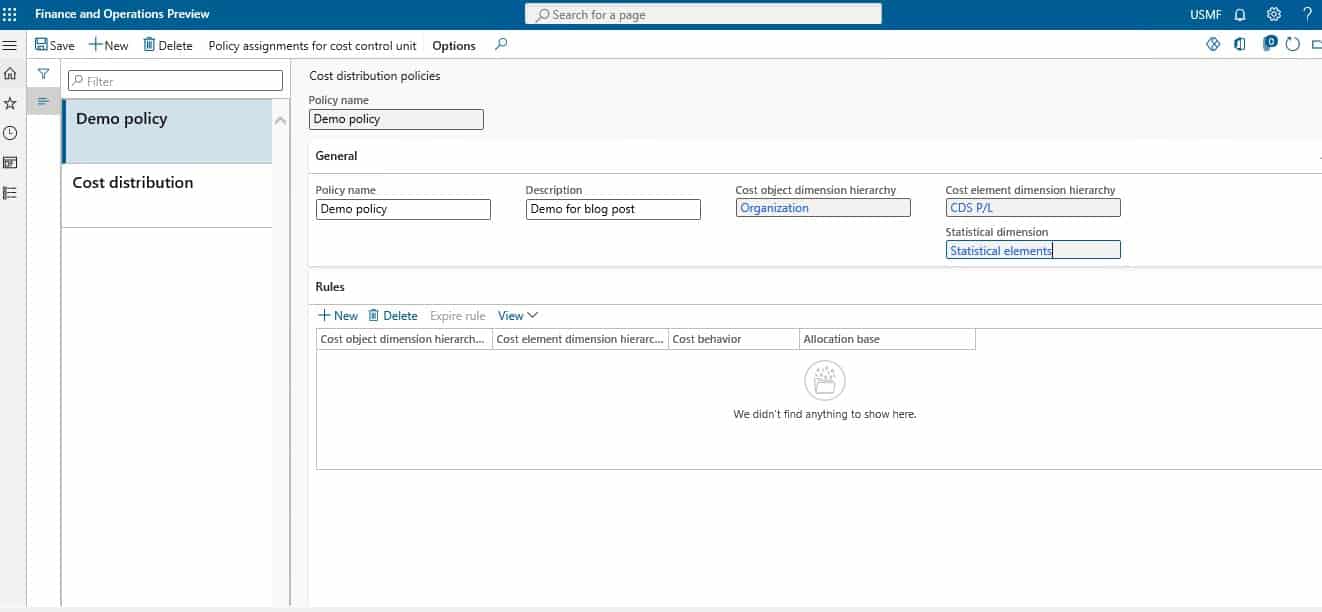
Create rules for the policy
Step 4
Click new on the rules tab.
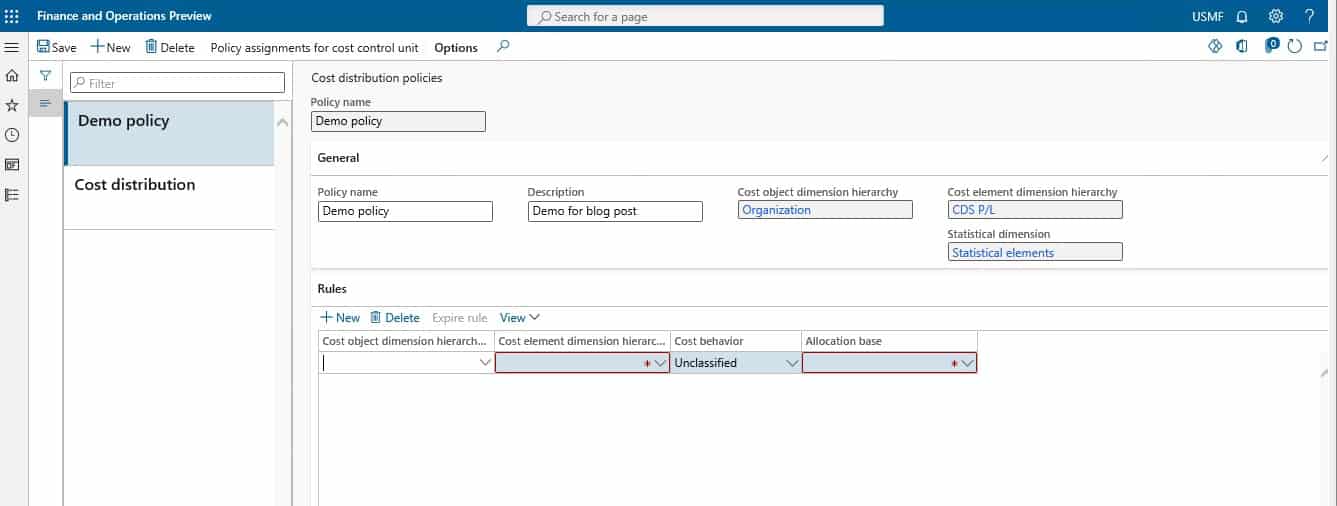
Step 5
In the Cost object dimension hierarchy node field, enter or select a value. Expand the hierarchy to select 094. Enter or select a value in the Cost element dimension hierarchy node field. For example, select Other operating expenses and then select 605110 Cleaning. In the Cost behavior field, select an option. Select Fixed cost. In the Allocation base field, enter or select a value.
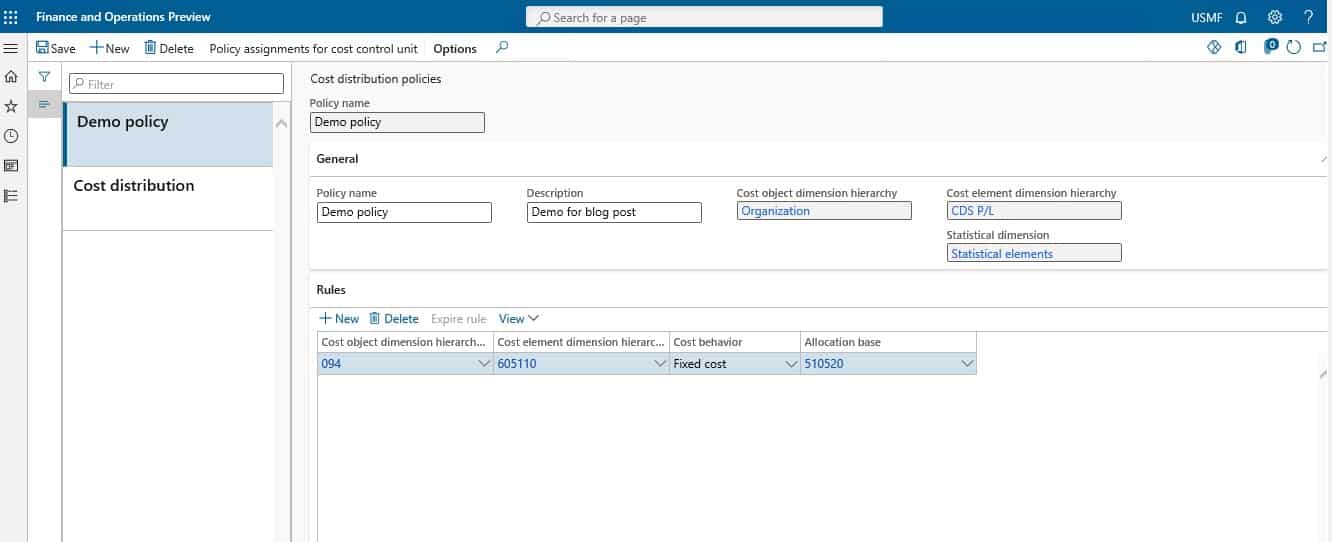
Step 6
Click new.

Step 7
In the Cost object dimension hierarchy node field, enter or select a value. Expand the hierarchy to select 094. In the Cost element dimension hierarchy node field, enter or select a value. Select Other operating expenses and then select 605150 Rent. In the Cost behavior field, select an option. Select Fixed cost. In the Allocation base field, enter or select a value. Click Save.
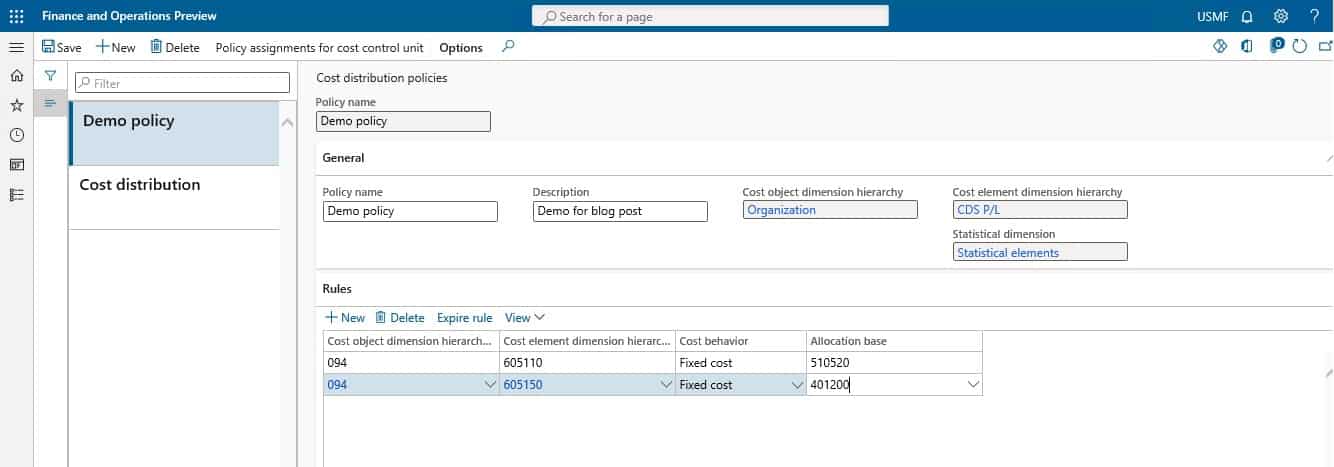
Step 8
Click Policy assignments for the cost control unit. Now we click on Add under Billing rules to add a rule to the list.
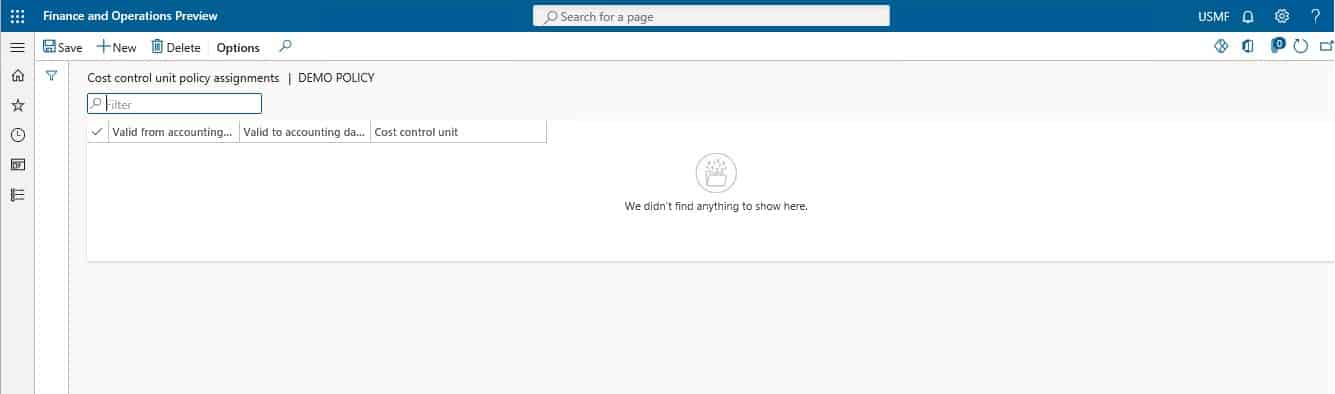
Step 9
Click New.
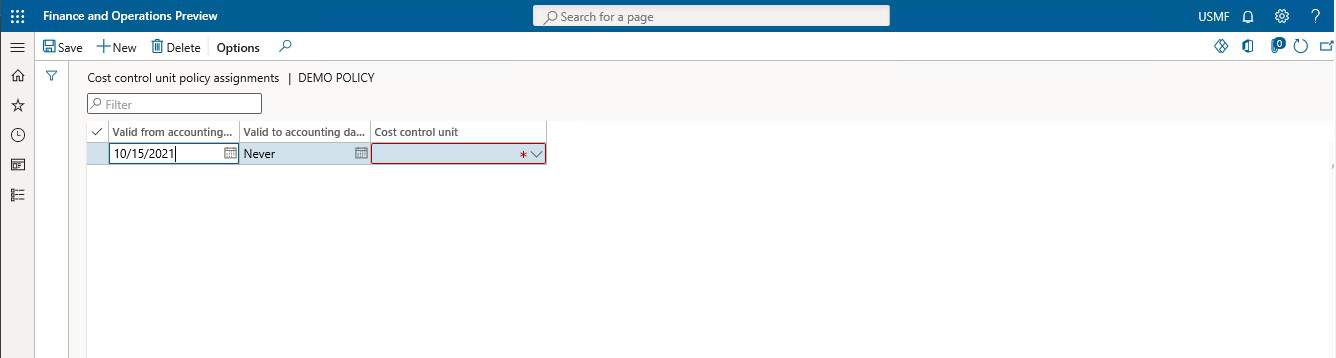
Step 10
In the Valid from accounting date field, enter a date. In the Cost control unit field, enter or select a value. Click Save.
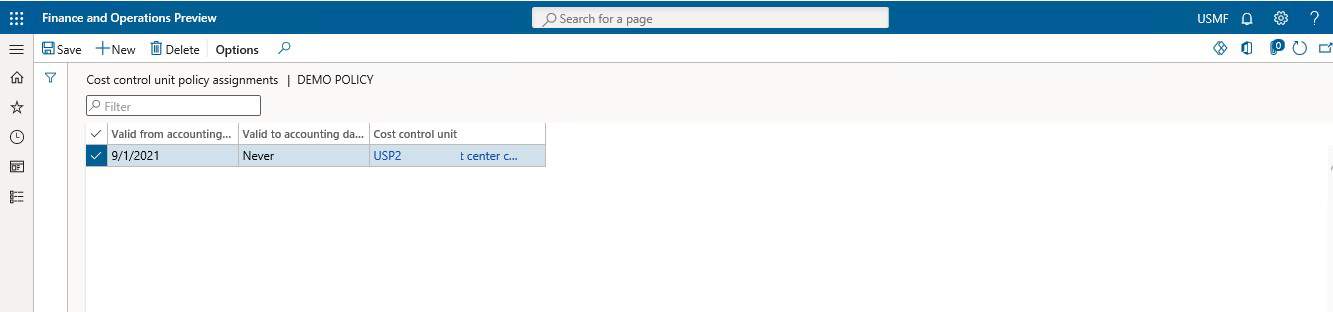
SUMMARY
Cost distribution rules are to disperse expenses that have been accounted for financially on a group of cost centers. First, the cost accountant ensures that the cost is allocated to the cost centers according to chosen allocation. Then, a cost control unit is given a policy and the regulations that go with it. The above task guide shows how to design a cost distribution policy and the rules that go with it using an example.
How to Minimize Distribution Cost?
Every company’s goal should be to cut distribution costs as much as possible. It will enable it to make the most money possible. To survive the pricing war, a corporation would also aim to reduce its distribution costs. You can use the following methods to lower a company’s distribution costs:
- A corporation may save a lot of money by avoiding tiny shipments. For example, a corporation can deliver one large package instead of many small shipments.
- The increasing quantity of sales returns is often one of the essential drivers for increased distribution costs. As a result, to regulate and minimize expenses, a corporation should seek to lower sales returns.
- A company should not rely on a single logistics provider. Instead, it should constantly negotiate conditions with the logistics supplier to receive the most effective rate.
- Technology, equipment, and work automation might also assist a corporation in lowering its distribution expenses.
- Performing a comparative study of demand and determining how urgently the consumer requires assistance will also be beneficial.
- Firms can also reduce the cost type distribution by avoiding the storage of finished items for extended periods. In other words, manufacturing is so well coordinated that the delay between production and dispatch is kept to a minimum.
Distribution Cost Minimization | |
Cost | Minimization |
Transportation cost | One large shipment instead of several small ones |
Increase sales quantity | Regulate expenses & seek lower sales returns |
Seek multiple logistic providers | Negotiate conditions with a logistic provider or consider new ones |
Work automation | Shift to automation tools like Dynamics 365 |
Perform comparative Study | Acknowledge the urgency of consumer requirements |
Well-coordinated manufacturing | Avoid finished item storage for long periods |
SUMMARY
A business must strike a balance between distribution expenses and product demand. The company’s goal should be to reduce distribution costs as much as possible. For this, the corporation must do a comparative study to determine how urgently the product is needed and whether or not it would result in sales losses.
At Instructor Brandon | Dynatuners, we always seek innovative methods to improve your competitiveness and suit your Microsoft Dynamics 365 requirements. Our offerings are founded on defined procedures, industry experience, and product understanding. If you’re interested to consult with our technical solutions experts on how we can help you define and create distribution policies or if you are having trouble finding the exemplary aspects for your cost distribution in Dynamics 365, we are here to tune it in the right way so it may fit your requirements, to get more information on it Contact Us.
[sc_fs_multi_faq headline-0=”h2″ question-0=”How to calculate cost per unit of distribution?” answer-0=”To calculate the cost per unit, add all of your fixed costs and all of your variable costs together and then divide this by the total amount of units you produced during that time period. ” image-0=”” headline-1=”h2″ question-1=”Is distribution cost a fixed cost?” answer-1=” A variable cost is the price of raw materials, labor, and distribution associated with each unit of product or service you sell. Whatever you pay to create each unit falls under the heading of variable cost. ” image-1=”” headline-2=”h2″ question-2=”Why is cost control important?” answer-2=”The main benefit of putting cost controls in place is lowering your company’s overall expenses. You can limit the amount of money different team member levels can spend, keeping more money from going out the door. Cost control is an essential factor for maintaining and growing profitability. ” image-2=”” count=”3″ html=”true” css_class=””]