Set Up CTP Value for Delivery Date Control in Dynamics 365
Receiving Point | Order Settings | Forms of Transport | Delivery Date Control | Trade Setup
Numerous manufacturers use sales lead time as the foundation for claimed ship dates on sales orders, where it commonly refers to the assured lead time (in days) for shipping stocked or made-to-order items. It is the simplest method of controlling promise dates compared to other processes such as Available-to-Promise (ATP) or Capable-to-Promise (CTP) reasoning. The usage of sales leads time is governed by several company-wide and item-specific regulations, each of which affects the ship dates for sales orders and sales quotations. Additionally, it necessitates the alignment of S&OP (Sales and Operations Planning) methodologies to fulfill order commitments and provide the appropriate degree of customer care. Sales order delivery date logic may be very beneficial in assisting your customer support employees in determining possible delivery dates for produced or made-to-order goods, hence helping you manage your client’s delivery expectations.
CTP
The CTP logic first evaluates the available inventory balance for the made-to-order goods. If none are accessible at the moment, the logic will then burst the BOM/Formula lines to examine the following: Components included in the BOM/Formula are readily available. Lead times for essential components when no stock is available Route “Run Time“ is a value given to the BOM/Formula. On the resource’s calendar, time is allotted for work. The determined (CTP) lead time is automatically computed in the desired ship date field on the Sales order line There are a few requirements and some basic setup needed to operate appropriately: In Master Planning Parameters, a dynamic master plan is assigned. Coverage groups in master planning have the ability to receive future communications. Moreover, assigning a Coverage Group to the Item’s Default Order further leads to configuration Creation of Resources with Approval and Activation of Calendar Routes Approval along with the activation of the BOM. This article provides an overview of CTP in the Dynamics 365 environment, including examples, limitations, and distinctions from available-to-promise (ATP).
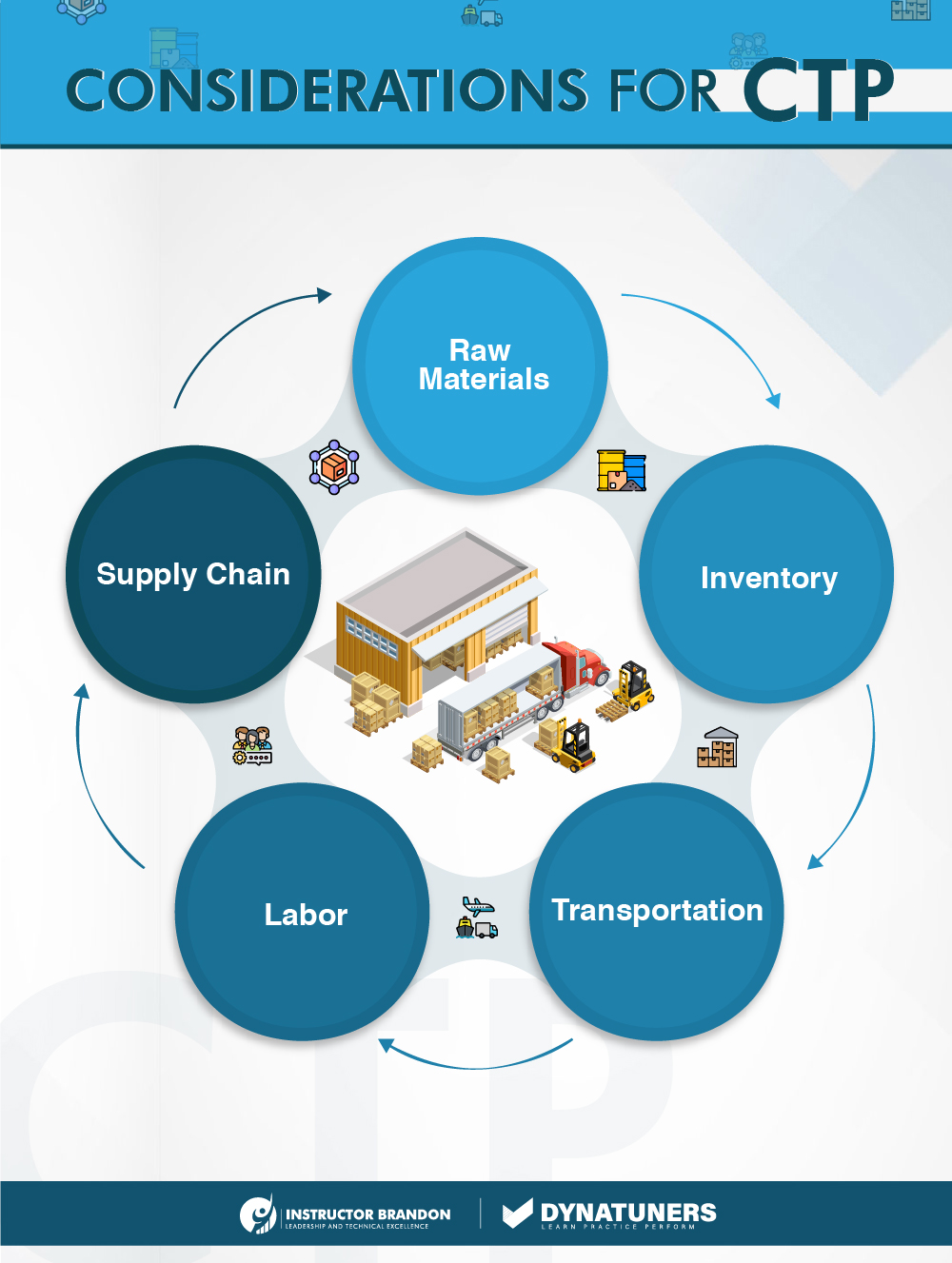
SUMMARY
Date logic for sales orders may be quite valuable in supporting your customer care workers. CTP is controlled by a number of corporate- and item-level rules. The determined (CTP) lead time is automatically calculated in the Sales order line’s intended ship date column.
Capable-to-promise (CTP) Process
Capable-to-promise (CTP) is the process of committing orders concerning available capacity and inventory. This procedure may include the establishment of various production or distribution facilities. CTP is also useful to establish the earliest possible delivery date for new or unplanned client orders. It determines when an item can be completed using a finite-scheduling model of the production system. Moreover, it incorporates any limits on manufacturing, such as resource availability, lead times for raw materials or acquired components, and needs for lower-level components or subassemblies. The delivery date results take production capacity, the existing manufacturing environment, and future order obligations into account. The goal is to decrease the time that production planners spend expediting orders and changing plans due to erroneous delivery-date assurances.
What is Available Capacity? Available capacity is the process of determining a unit’s ability to complete a specific job within a specified time. The capacity to produce a projected output varies by industry. First, the available capacity must be determined concerning the business. Then, it can work in terms of volume and compare it to the firm’s standard available capacity. A business may assess the capacity of individual resources or a collection of resources. The procedure aids in the overall planning of the company and inventory management. Do you want to learn more on how to handle multiple delivery schedules for single order lines, read our blogs.
Available-to-promise – ATP refers to the amount of an item that is available and can be guaranteed to a buyer on a certain date. The ATP computation takes into account unsold goods, lead times, scheduled revenues, and difficulties. Calculate the amount of ATP using the “cumulative ATP with look-ahead” approach. The primary benefit of this ATP calculating approach is that it is capable of handling situations in which the aggregate of problems between receipts exceeds the most recent receipt. The ATP quantity is equal to the first period’s uncommitted inventory balance. Typically, it is computed for each planned receipt period. The program determines the ATP period in days and uses the current date as the starting point for calculating the ATP amount. ATP contains on-hand inventory less client orders that are due and late in the first period.
Differences between Capable-to-promise and Available-to-promise
How is Available-to-promise (ATP) calculated? It is a concept used in sales and operations planning to describe the absolute number of items or services available for shipment to customers at any particular moment, fewer quantities held by or committed to other customers.
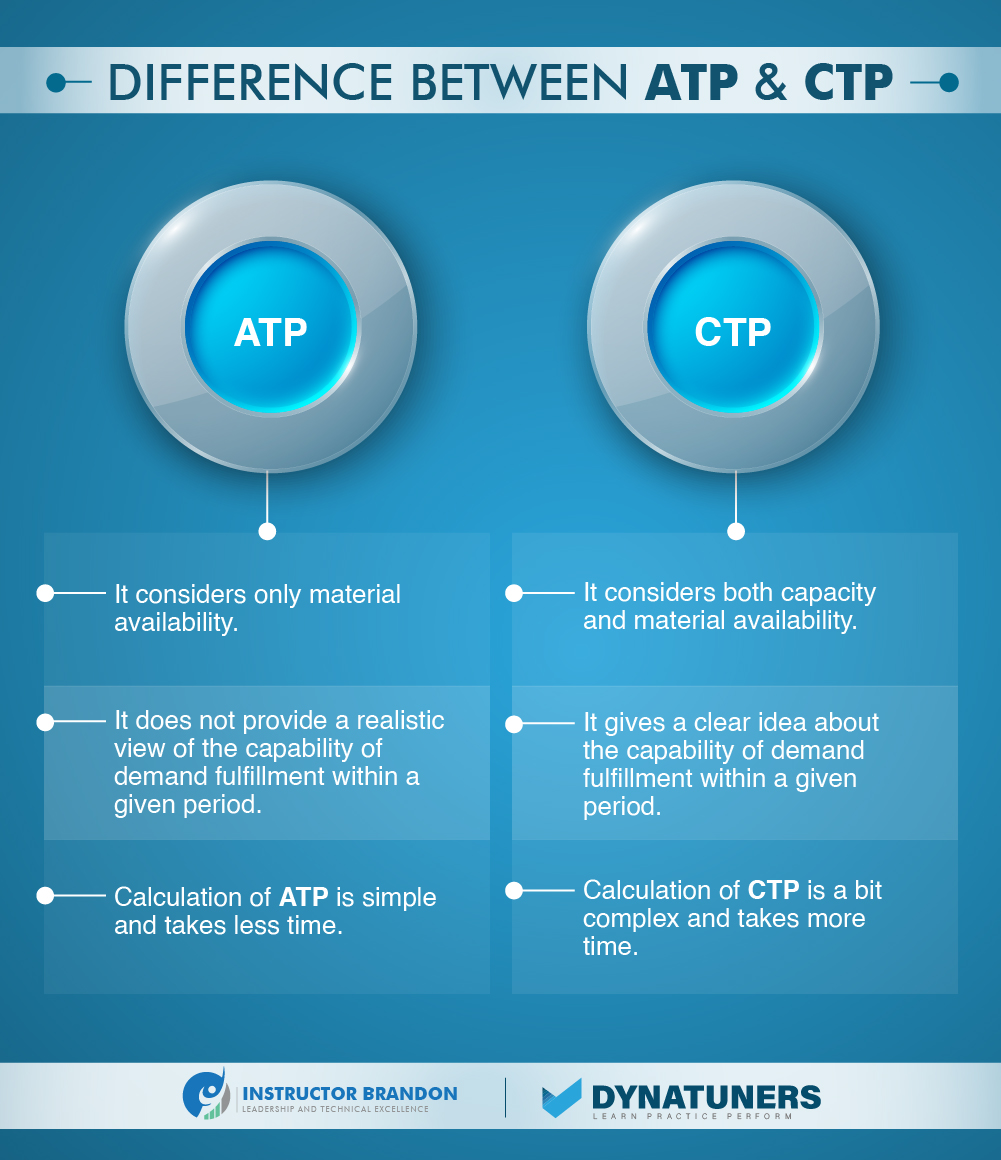
SUMMARY
CTP is a term that refers to the process of committing orders based on available capacity and inventory. The term “ATP” refers to the quantity of an item that is available for purchase and can be guaranteed to a customer on a certain day. CTP calculations take longer than standard ATP calculations. Additionally, the distinction between ATP and CTP has also been highlighted.
Example of Capable-to-Promise
In manufacturing, a corporation commits to providing a product on time and according to specification. This demonstrates that the organization has the resources necessary to deliver on its promise and its confidence in its ability to create a high-quality product. When a business makes a CTP guarantee, it stakes its reputation. As a result, companies must make only promises they are confident they can meet. This way, consumers and suppliers may have faith in the production process and the company’s ability to provide high-quality goods on time. For example, assume that X is the end product and that Y and Z are the components necessary to manufacture X. Assume that the quantity of product X on hand is zero. In this scenario, if you do ATP, it returns 0 since it merely verifies the material’s availability. When you do CTP, it demonstrates the availability of both materials and resources. Thus, it establishes the availability of components Y and Z required to construct the product X. Additionally; it monitors the number of items manufactured using these materials and resources. Additionally, it constrains the number of additional components Y and Z and other resources necessary to manufacture extra product X.
Calculating the optimal work hours is also very crucial. The hours of operation are critical in determining the unit’s output capacity. Breaks, technical problems experienced during working hours, and any other organizational challenges, on the other hand, might have a significant impact on working hours. Generally, cracks are subtracted from the operating hours. As a result, they are sometimes referred to as hypothetically available hours. The operational time is defined as the productive working hours achieved after subtracting technical and organizational issues.
Similarly, capacity utilization may determine the proportion of time spent in production by a unit. The version number refers to the discrepancies discovered when calculating the available capacity. Additionally, the actual version number is employed in scheduling and capacity planning. Are you ready to the next step in your career, check out our latest beginner and certificate level courses.
SUMMARY
In manufacturing, a business commits to delivering a product on schedule and as specified. When a firm guarantees CTP, it puts its reputation on the line. As the total working hours can be affected by breaks, technology challenges, or other organizational concerns, Calculating appropriate work hours are critical for estimating the production capacity of the machine.
Today’s Business Scenario, Industrial Applications and CTP
Nowadays, numerous businesses are attempting to alter their production planning and strategy to increase order fulfillment flexibility. Capacity and capability restrictions are critical variables in manufacturing, necessitating effective production planning to maintain a consistent service level and minimize inventory costs. Additionally, Dynamics 365 can be utilized as an Enterprise Resource Planning (ERP) system to direct CTP order processing techniques to maximize automated order handling efficiency.
Some leading manufacturers are using MTO (Make to Order) and BFS (Buy from Stock) flows. MTO is the main flow, both ATP and CTP are used in both flows for good customer orders. They use pure ATP and mixes ATP & CTP to promise orders having different order lines, which lead to other promising methods. In CTP, there is another check-called CTPCO which only inspects capacity, and not materials. While setting up CTP, the critical items are selected to be focused on to promise. The rest are just set up high. The low volume items’ CTP will be based on the forecast. CTP setting up is based on the forecast so far, considering capacity and materials. CTP level is set on customer order product or finished goods.
Sr. | Right Parameters for CTP for Delivery Date Control | |
Parameter | Description | |
1. |
Machine capacity | A load of machines is required by calculating run time, set up time, and cycle to get capacity hours per working day times.
Total capacity = amount of product x cycle time of machine x set up a time. |
2. |
Bottlenecks | The bottlenecks in production take the longest production lead time in operation. |
3. |
Labor capacity | This data calculates hours a day and working days, including available time and shifts, with a monthly perspective. Maintenance is part of the workload (running prevention rather than a correction). |
4. |
Utilization of machines | It is the output from the machine to see how much the machine can produce. |
5. |
Flexibility level | Flexibility is the extra capacity (Over/free capacity); for example, +60% of actual capacity means that the production capacity can increase the utilization up to 60%. This is the significant factor for setting CTP in VCE regarding a monthly planning basis. |
Some manufacturers may be attempting to balance buffering size (item maintenance fees) and goods to be sent. To create flexible CTP levels, there should not be too many constraints, and the production schedule should not be very detailed. This implies that you should avoid setting up a complete production schedule. Furthermore, it is critical for the system to improve data quality since stock quantities and lead times may be incorrect. Last but not least, essential items’ setup is vital. The capacity and available resources determine this configuration. Our professional consultants at Dynatuners react quickly to client demands through business automation, difficult integrations, or performance reporting. Following examination of CTP, master planners decompose the numbers, here CTP can be configured using forecasts, historical data, and actual orders.
The following statistics and analysis are used to make the CTP setting approach more reasonable:
- Global planning forecasts (Monthly basis).
- Historical data derived from prior demand.
- Current demand (Daily basis).
- Standard Module Consumption.
- Capacity and duration of production.
- Structure of the Bill of Materials
- Visibility of the material
- Lead and delivery methods of vendors.
- Constraints in establishing CTP.
SUMMARY
In production, capacity and capability constraints are significant factors. Many manufacturers prefer orders via MTO (Make to Order) and BFS (Buy from Stock) flow. Order promising in D365 increases the efficiency of automated order processing.
Stakeholders in Call to Promise
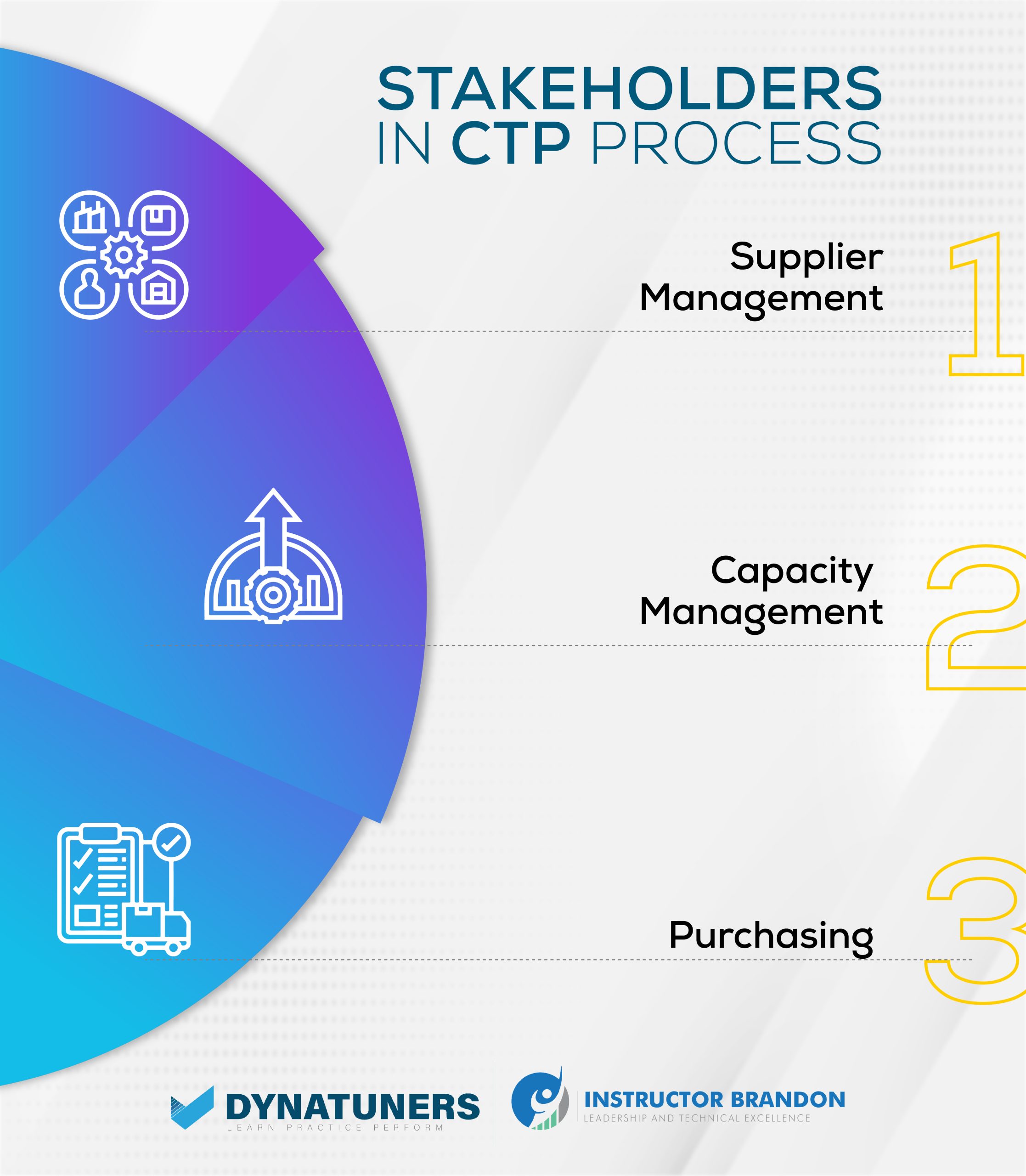
Each stakeholder’s involvement in the CTP process may be summarized as follows:
-
Supplier Management
Supplier planners with sufficient knowledge and expertise in supplier development should consider the supplier capabilities every month when determining the CTP level on bought standard modules.
-
Purchasing
Purchasers get immediate access to information on suppliers’ weekly responses. This implies they are aware of the material condition and the varying performance of each provider. That is why customers are responsible for daily updates to the CTP level of the standard module.
-
Capacity management (Dimensioning & Planning)
Master planners are responsible for calculating production capacity, establishing safety stock (buffer dimensioning), and other tasks within the Dimensioning & Planning department. CTP adjustment is a critical activity for master planners. By using the Dynamics 365 master planning and Planning Optimization, you may conduct analysis based on your present configuration and data.
SUMMARY
Above paragraph discusses the key stakeholders involved in CTP processes. Most critical includes supplier planners, purchasers, and key personnel managing capacity in production department.
Setting up CTP for Delivery Date Control in Dynamics 365
Process
Step 1
Go to Production Information Management > Products > Released Products.
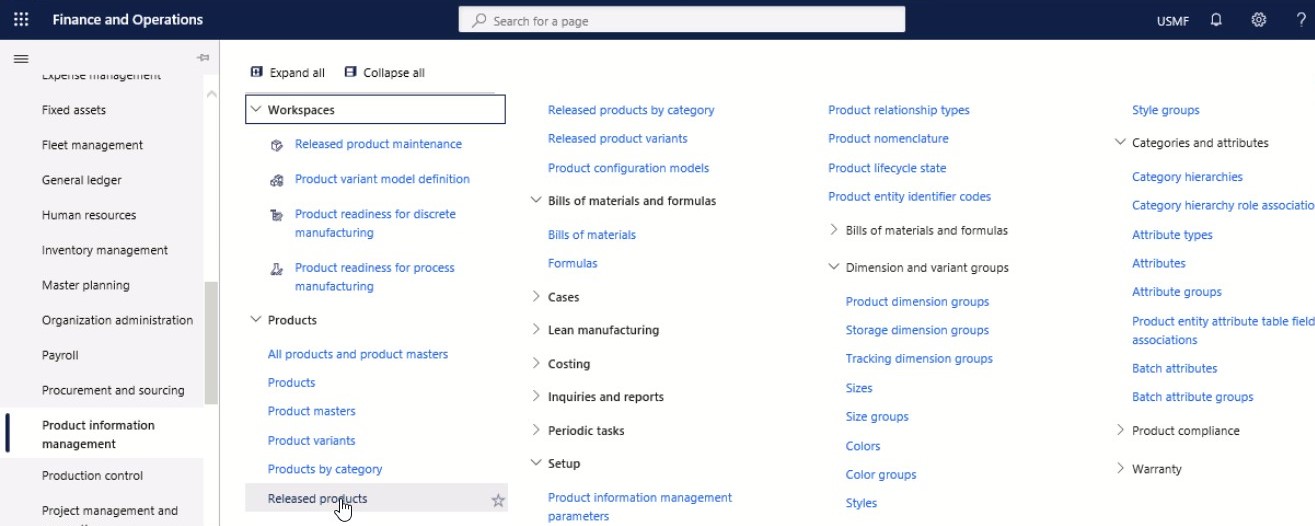
Step 2
Select the created item.
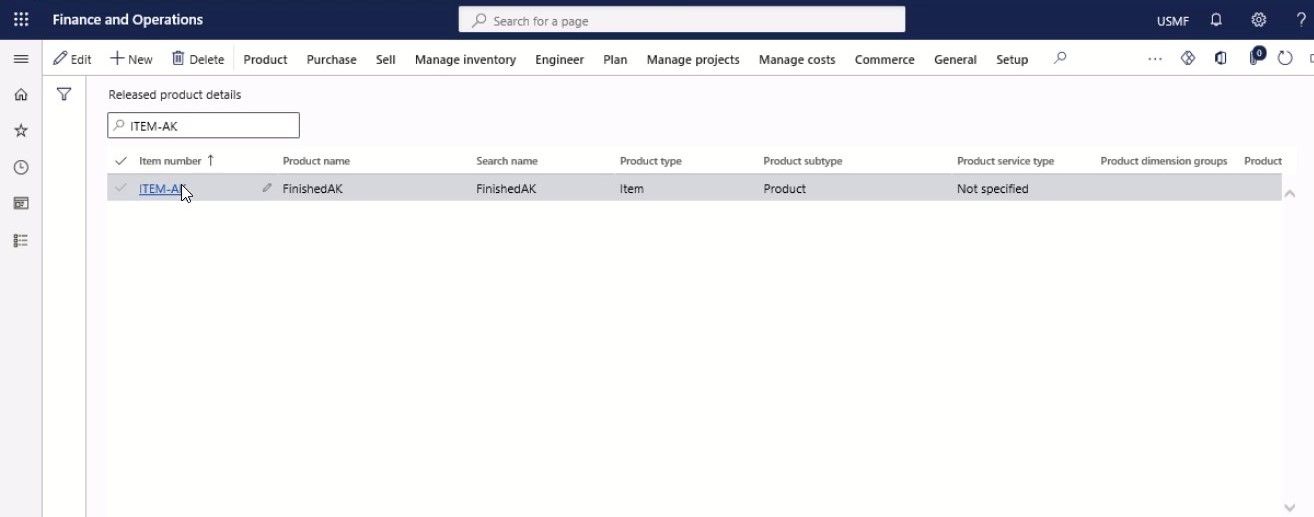
Step 3
Go to Manage inventory> View > On-hand inventory in the action pane.
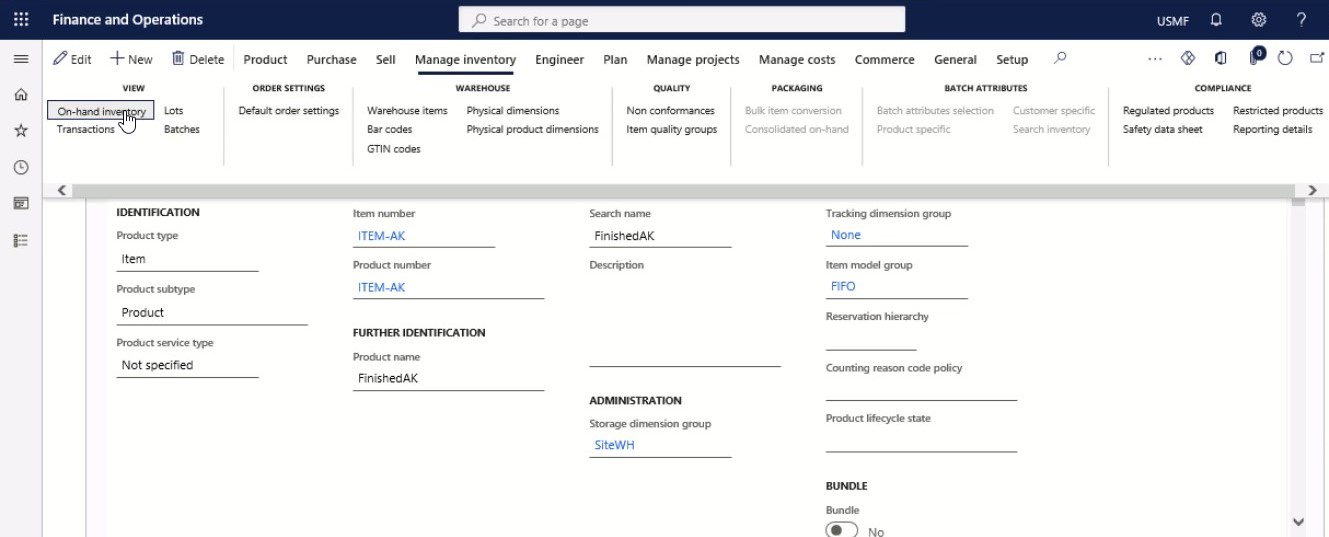
Step 4
Check current On-hand inventory for the manufactured item ITEM-AK. As you can see, there are currently no items present in the stock.
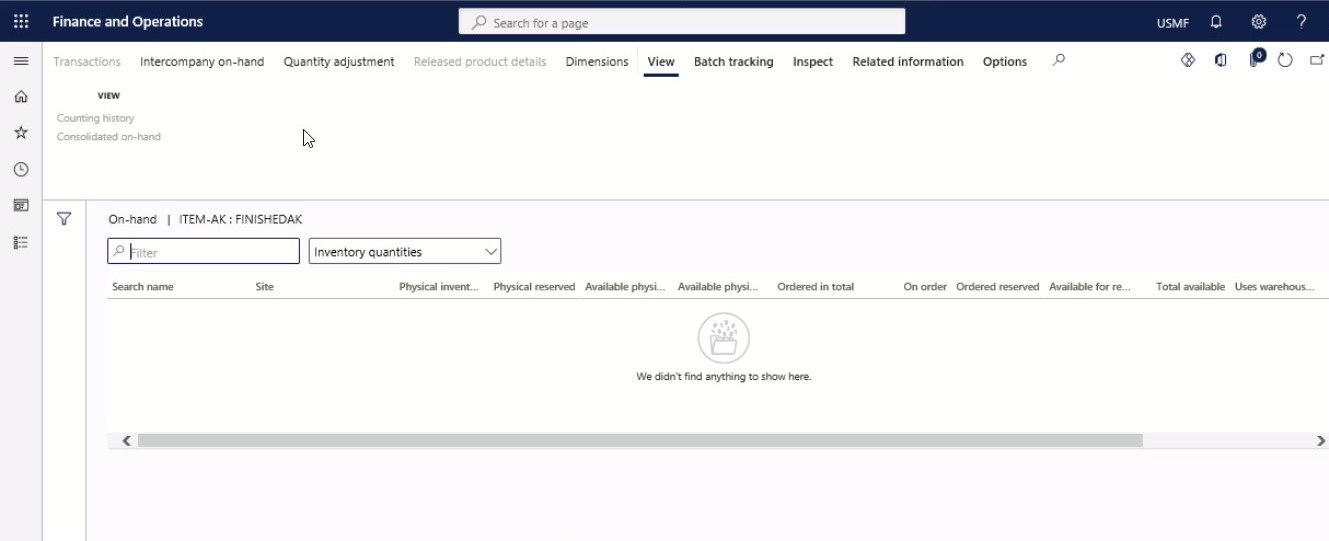
Step 5
Navigate to Accounts Receivable > Orders > All sales orders.
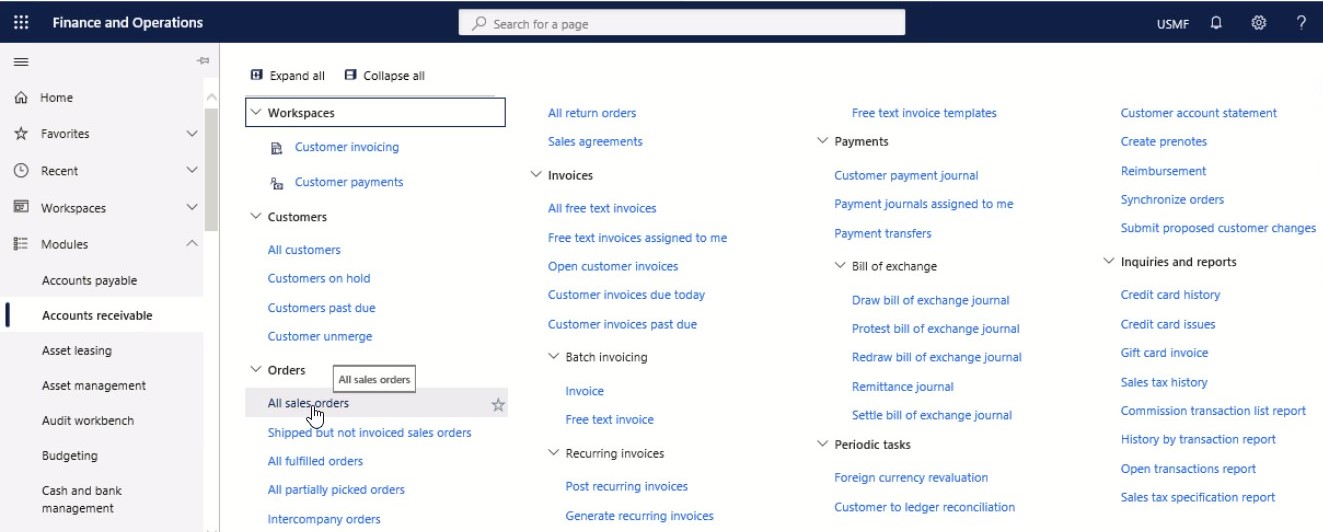
Step 6
Select New.
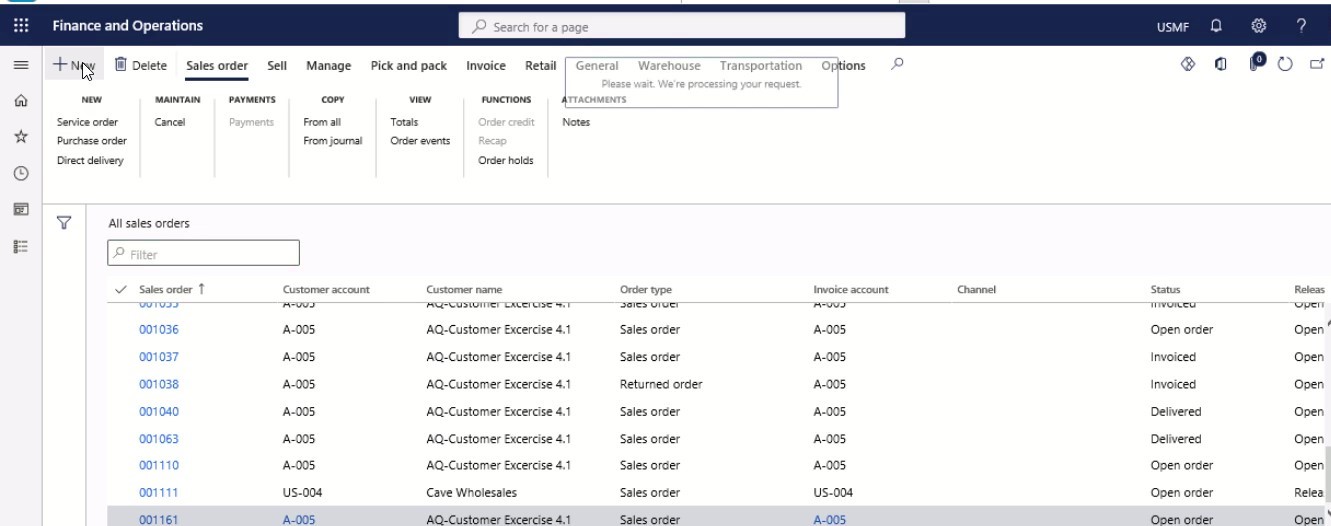
Step 7
Create new sales order for the newly created item ITEM-AK (2).
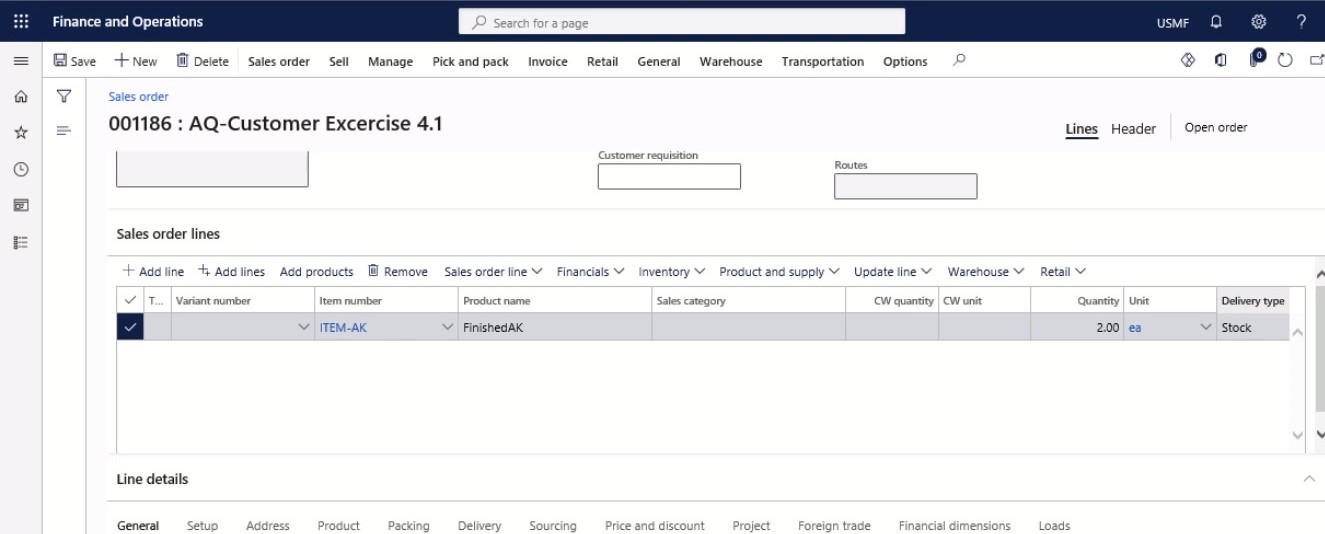
Step 8
Go to Line details Festa, click Delivery.
Step 9
Make sure the selected Delivery Date Control is CTP.
Step 10
Select the requested ship date and receipt date for today.
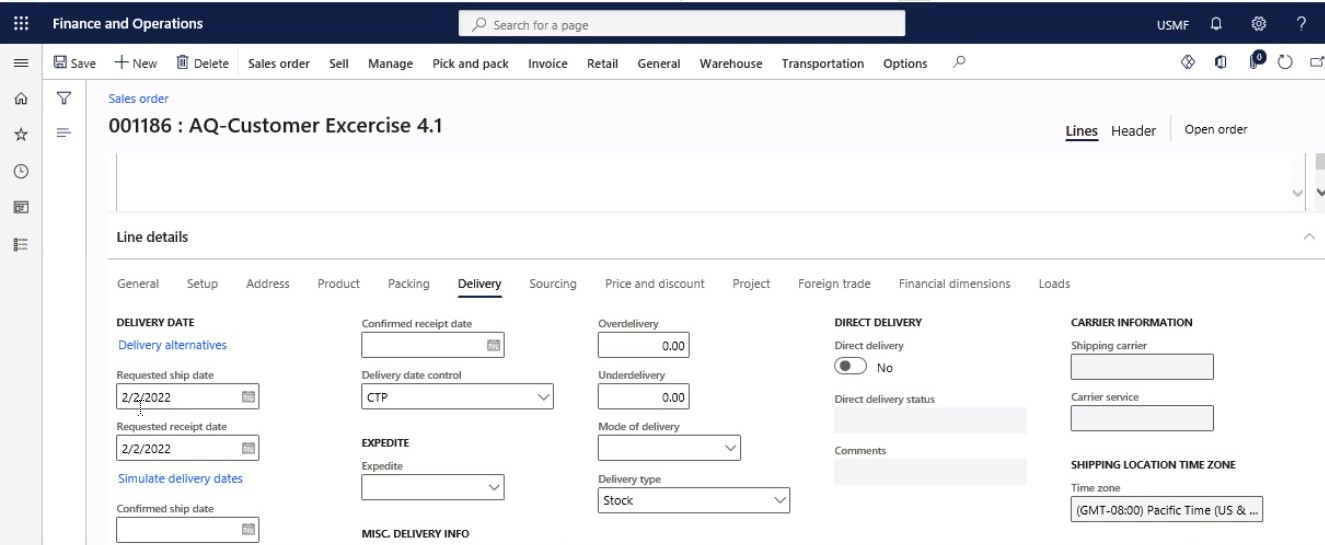
Step 11
Click Save.
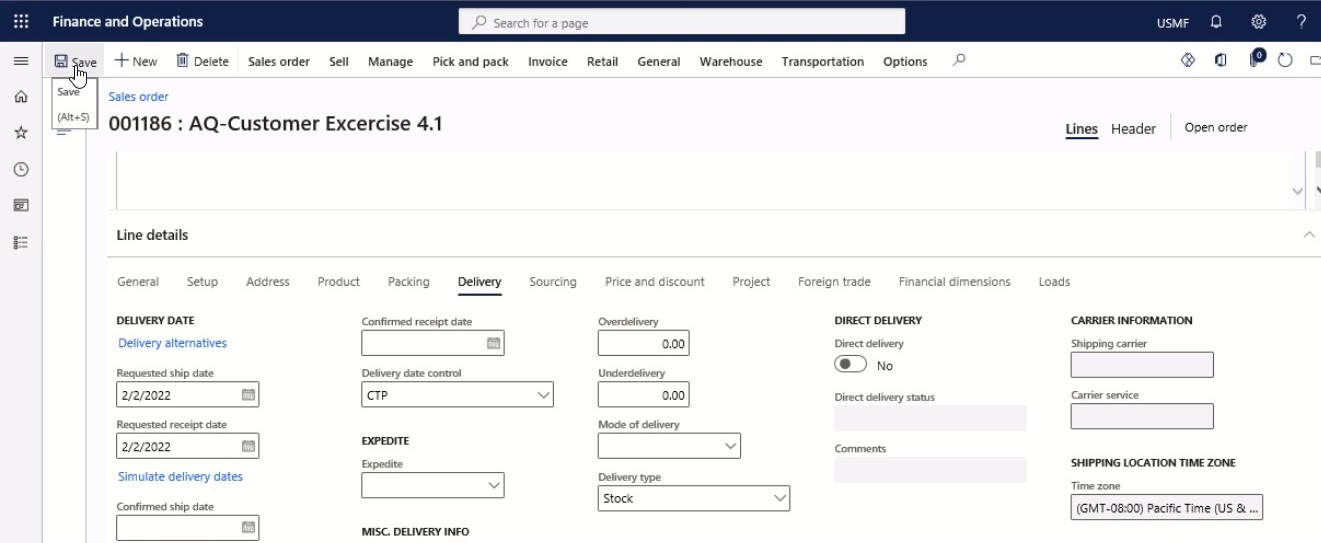
Step 12
Select Simulate Delivery Dates.
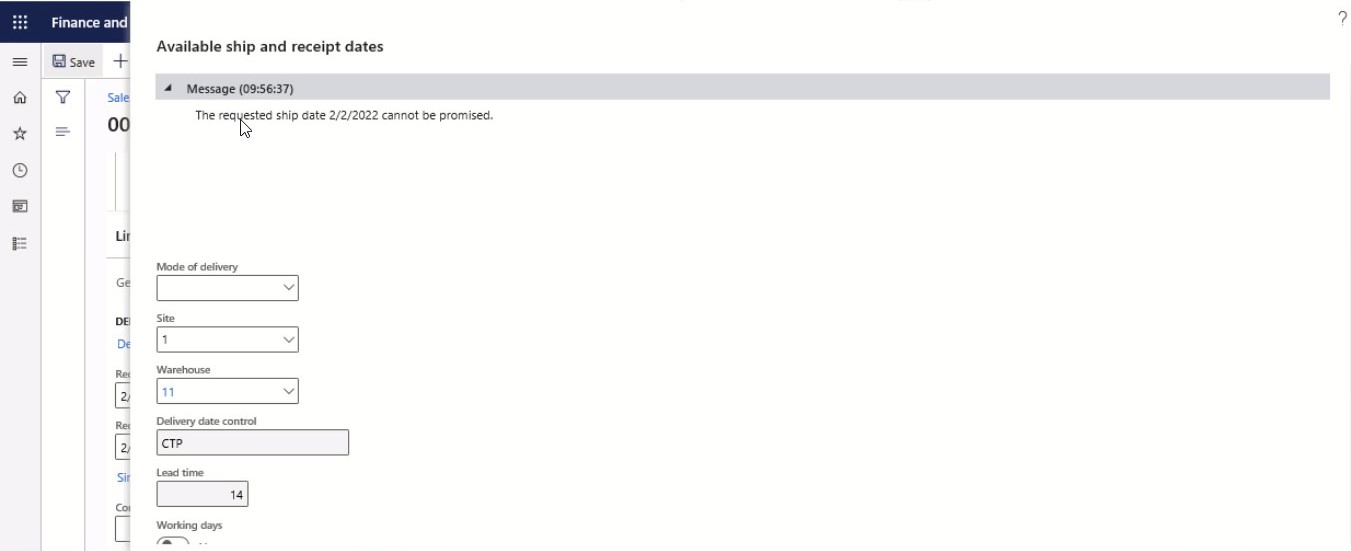
Step 13
The message says that the requested ship date cannot be promised because the items need to be manufactured. As it takes 40 hours and a resource works 7.5 hours per day, we will need 40 / 7.5 = 5.33 working days (> one working week) for one item.
Step 14
Available ship dates are mentioned in the same pop-up below.
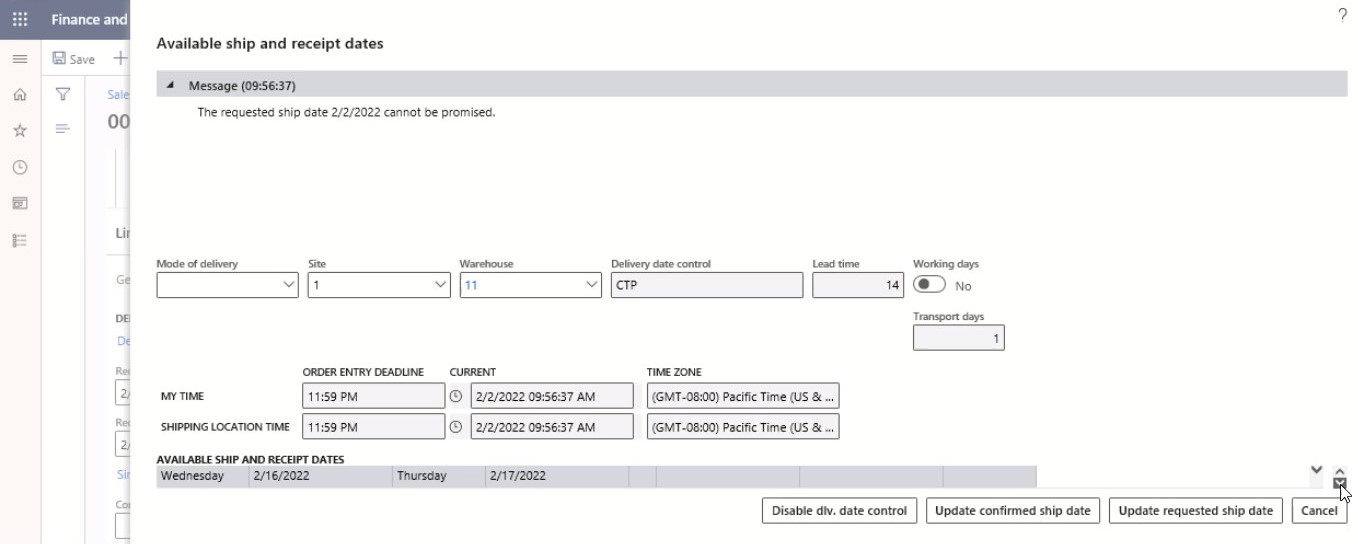
SUMMARY
Following the above process, you can set up CTP values for delivery date control in D365.
Final Thoughts: Delivery Date Control
Dynamics 365 CTP functionality enables you to reliably guarantee and keep delivery dates to your clients. Order Promising is a feature in D365 that determines the earliest ship and reception dates based on the delivery date control technique, including the number of transport dates. You may choose between four distinct techniques for controlling delivery dates: sales lead times, ATP or available to promise, ATP + issue margin, or CTP, competent to promise, for manufacturing staff.
Capable-to-promise is a worldwide lens through which demand and capacity are seen. Numerous aspects contribute to the success of this kind of system, including raw materials for goods, inventory management, transportation, labor, and supply chain management. A CTP system can provide precise forecasts about what is achievable inside the organization by examining these factors. Looking to select the right certification for yourself, if you have any questions, contact us at help@instructorbrandon.com.
Capable-to-promise is only one example of an enterprise solution that uses data analysis to assist organizations in solving difficulties. Cloud computing and other technological advancements have provided organizations with very sophisticated data analysis and forecasting tools, which they are using to improve customer service, optimize corporate operations, and operate at optimum efficiency. However, due to the unpredictable performance of suppliers, evaluating the CTP setting is challenging. As a result, it is critical to design an efficient instrument or approach for measuring suppliers’ performance since their performance varies significantly weekly or monthly. As a result, the CTP level may be modified weekly in response to supplier performance to get the most reliable CTP level to measure supplier capabilities.
At Instructor Brandon | Dynatuners, we always seek innovative methods to improve your competitiveness and suit your Microsoft Dynamics 365 requirements. Our offerings are founded on defined procedures, industry experience, and product understanding. If you’re interested to consult with our specialists on how to Setup CTP Value for Delivery Date Control in Dynamics 365 SCM, don’t hesitate to Contact Us.
How are ATP and CTP different?
Whereas ATP evaluates just material availability and makes the assumption of limitless capacity resources, CTP includes both material and capacity availability, providing a more realistic view of whether demand can be met within a certain time period.
What is CTP in terms of supply chain management?
Capable to promise CTP solutions allow businesses to commit to customer orders based on available or projected production/resource capacity and inventories available or planned.
What are ATP and CTP, and what are their applications?
ATP is a measure of the balance between planned and actual supply and demand. You may utilize ATP data to evaluate how much more product you can offer to clients. Component CTP and capacity CTP are extensions to conventional ATP that are used to establish the maximum number of items that may be produced in addition to those already planned.